Architectural Cast Stone: Enduring Beauty and Strength
Words: Sarah Mathews
Words: Sarah Mathews, President and Owner, Midwest Cast Stone of Kansas, Inc. (“Midwest Cast Stone”)
Photos: Midwest Cast Stone and as credited.
With many choices for building materials, why select architectural cast stone? Let’s start with a general understanding of architectural cast stone, also known as cast stone.
What is Architectural Cast Stone?
Architectural cast stone is a man-made versatile building material that replicates the appearance and texture of natural stone. Its strength, customizability, and endurance has made cast stone a sought-after material in construction dating back to ancient civilizations.
Ancient Egyptians used cast stone for sculpting intricate artworks, while the Romans adopted it to construct their grand aqueducts: remnants of both still stand today. During the 19th century, advancements in mixing and molding techniques created a surge in its popularity in London as well as the U.S. The 1920s and 30s, in particular, saw architectural cast stone becoming the material of choice for many significant structures due to its versatility and durability. And its popularity continues into the 21st century.
Belmont Village - Original Piece To Be Replicated
Belmont Village - Replicated Piece Ready For Curing
At its core, architectural cast stone is an exceptionally refined architectural concrete unit. Designed meticulously to imitate natural stone such as limestone, sandstone, granite, and travertine, cast stone consists of fine, natural aggregates mixed with cement. These components, when coupled with coloring pigments and chemical admixtures, result in a versatile material that is not only structurally sound and long-lasting but also aesthetically pleasing.
Cast stone is commonly used to provide modern and traditional architectural design-enhancing accents, trim, ornamentation, or functional features on buildings or other structures. It is used for commercial, residential, and hardscape purposes. Typical elements consist of window sills and window and door surrounds; wainscot, transitions, coping and banding; pier caps, column caps, and wall caps; veneer and accent panels; cornices, capitals, and medallions; columns, balustrades, and railings; arches and keystones; address blocks; and imbedded or stand-alone signage. Here is an example of a home without cast stone and with:
Graphics Credit: Midwest Cast Stone
Setting the Architectural Cast Stone Standards
One of the unique attributes of cast stone is the industry standards that regulate and govern its production, application, and maintenance. These standards ensure a consistent product for all parties. They also provide a standard to which manufacturers and installers may be held accountable:
- ASTM C1364: This standard acts as the backbone for architectural cast stone. By establishing requirements for permissible component materials, the processes of sampling, and testing methodologies, ASTM C1364 creates a quality baseline that manufacturers and contractors must adhere to. The International Building Code, beginning in 2012, references ASTM C1364 as the definition for architectural cast stone.
- The Masonry Society Standards: The International Building Code, beginning in 2018, adopted the following architectural cast stone standards as legally binding in jurisdictions where adopted.
- TMS 404: This standard addresses the design of cast stone units.
- TMS 504: This standard addresses the fabrication of cast stone units.
- TMS 604: This standard addresses the installation of cast stone units.
- Master Format Specification 047200: A more detailed blueprint than ASTM C1364, Specification 047200, is typically “cut and pasted” into Project Plans and Bidding Documents as the contractual specification for architectural cast stone. Spec 047200 delves deep into product standards, providing extensive requirements and guidelines for the fabrication and installation of architectural cast stone.
Selecting the Best Cast Stone Manufacturer for Your Project
There are many manufacturers of cast stone in the United States alone. How do you decide which one to partner with? Here are some tips for ensuring you are selecting the best one for your specific job.
1. Choose a Cast Stone Institute-Certified Producer Member
The easiest way to ensure the cast stone industry standards are being met by the manufacturer of your project’s cast stone is to select a manufacturer that is a Producing Member, in Good Standing, of the Cast Stone Institute (CSI). The Cast Stone Institute stands as an authoritative body in the realm of architectural cast stone. By defining and upholding high standards, the CSI ensures that its members produce and supply top-tier products. Architects, General Contractors, and Owners often require that any manufacturer being considered as a project partner be certified as a producing member of the CSI, and it is a standard requirement of Spec 047200.
Partnering with a manufacturer that is CSI-certified offers:
- Assured Quality: Regular and rigorous product testing data submittals as well as unannounced plant audits guarantee that certified members are strictly adhering to the latest industry standards, thus ensuring a top-tier product.
- Continual Improvement: Members are required to undertake regular training, ensuring they remain at the forefront of the latest industry innovations, technologies, methodologies, and best practices.
- Longevity & Reliability: The standards upheld by CSI members ensure that the products are not just of high quality but also guaranteed durable and reliable with minimal maintenance, backed by a Limited Warranty.
To become a Producing Member, manufacturers must meet stringent criteria demonstrating experience in manufacturing architectural cast stone, the ability to produce material that conforms to the relevant standards consistently over time and pass a manufacturing plant inspection. To maintain membership and manufacturing excellence status, producing members must adhere to the CSI’s Code of Ethics, submit to unannounced plant inspections to ensure compliance, and continue to participate in CSI’s Certification Program. This includes submitting regular product testing results (conducted by each manufacturer and verified regularly by independent testing laboratories) for all required final product characteristics that prove the standards are met or exceeded. Note: Some manufacturers identified as CSI-certified in bid document specifications are outdated and invalid. Please verify that a manufacturer you are considering is listed as Active and in Good Standing on the CSI website, www.caststone.org, which is updated regularly. Manufacturer-specific testing data and certification is available directly from each of the CSI Member Producers.
2. Ask the Tough Questions
Choosing a CSI-certified manufacturer or deciding you don’t need the assurance CSI certification affords isn’t the end. Cast Stone manufacturing, by any of the three methods approved – Wet Pour, Vibrant Dry Tamp (VDT), and Block/Tier Stone Machine – is an exacting, laborious, hands-on process, with unique adjustments made at each plant and by each manufacturer. Additional questions to ask your prospective manufacturer are:
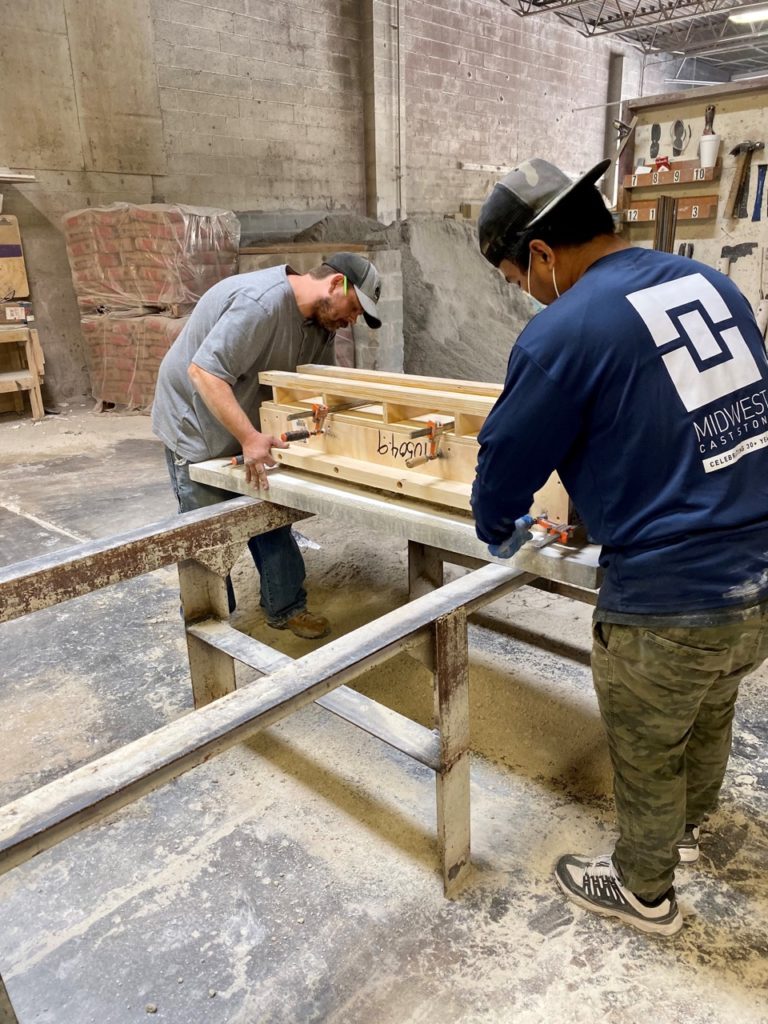
- Manufacturing Method: How does the manufacturer produce, and what percent is cast stone of total manufacturing? This is an important question to assess the manufacturer’s commitment to producing high-quality cast stone. For example, at Midwest Cast Stone, we produce solely via the VDT method to ensure the highest Quality Assurance and Quality Control over all aspects of the design, fabrication, production, and curing/finishing/packaging process. The dry tamp method involves compacting a zero-slump, low-water-content mixture into a mold under intense pressure, ensuring that there is a consistent density and texture throughout the stone. After demolding, the stone is cured prior to packaging.
- Pre-Production Services: Who provides the manufacturer’s pre-production services? For example, are Estimating and Take Off drawings prepared by the manufacturer’s trained staff in-house? Or are they done by third-party commercial estimators? If this work is done in-house, the manufacturer is in a better position to propose cost-saving design alterations upfront. Is the manufacturer limited to only Delegated Design work, or can the manufacturer’s in-house team support Design Build projects? At Midwest Cast Stone, we conduct all pre-production services ourselves, from Estimating and Bidding to TakeOffs to Shop Drawings to Mold Fabrication. We believe it’s best to choose a manufacturer who can support both delegated design and design-build work, if not for the project at hand, then to have that capability in the future once you’ve established a good relationship with the manufacturer.
- Product Curing: The cast stone standards require that each unit be cured prior to shipping and installation. Curing can be achieved either by “Yard Curing” – leaving the just-produced units to cure in place in a 95 percent moist environment at a minimum of 70ºF for 16 hours after casting, or by placing just-produced units in a warm curing chamber approximately 100ºF at 95 percent relative humidity for approximately 12 hours. This preliminary curing is then supplemented with additional yard curing at 95 percent relative humidity for seven days @ 50°F or five days @ 70°F prior to shipping. This required “wait” time means that the product cannot be produced and shipped as quickly as may be needed by the installing mason, say, if a piece breaks during installation and a replacement is needed. That’s why you will want to ask how your prospective manufacturer cures its cast stone. At Midwest Cast Stone, as well as a few other manufacturers in the U.S., we have invested in the latest curing technology that enables us to produce and ship ASTM-compliant stone faster. The latest testing by Kraft Curing shows that CO2 vapor accelerates cast stone curing, and also ensures harder corners and edges, reduces hazing, produces constantly consistent colors, and higher early strengths. We’ve found our Krat Curing system to be a game-changer for our customers who need a replacement piece the next day or when a project is a Rush job overall.
- Customer Service: Who will you be able to contact at any point once the contract is signed to ask questions about your project? Preferably, you’ll have one point of contact from cradle to grave. Also, does the manufacturer provide training on best practices for handling and installing the supplied cast stone at the jobsite? While cast stone is very durable, rough handling can result in chips and cracks that need to be patched. While each manufacturer will supply a “Patching Kit” along with finished product, even the best-applied material patches may have a different texture and a slight color variation from the original unit. The best way to avoid the noticeability of a patch is to not need it in the first place, and that’s where masonry installation tips, as well as education on TMS section 604, is an important part of the manufacturer’s customer service. The same goes for education on best practices for cleaning and sealing cast stone at the end of the overall masonry project. Only cast stone-safe cleaning products should be used, and special care should be taken if cleaning brick or stone adjacent to installed cast stone units. Regular every-10-year cleaning and sealing should be made part of the building or structure’s ongoing maintenance plan as well. Your manufacturer should have all of this information ready and available to share with you.
To summarize, cast stone has been chosen and used for thousands of years. Its ability to replicate the elegant and timeless appearance of natural stone, combined with its longevity, makes cast stone a favorite choice for many architects, general contractors, builders, masons, and owners. And when produced by a manufacturer certified by the Cast Stone Institute, it is guaranteed to provide a seamless blend of functionality, aesthetics, and cost-efficiency.