Marvelous Masonry - Celebrating Masonry’s Heritage: The Ancient City of Gordion
Words: David Biggs
Words and Photos: David Biggs, PE, SE
Masonry is the only building material that has survived millennia and helps define our cultural heritage. We all know of such iconic structures as the Pyramids in Egypt, the Roman Colosseum, the Taj Mahal in India, Washington Monument, the Parthenon in Athens, Machu Picchu in Peru, the Haga Sophia in Istanbul, and more. In addition, there are fantastic archeological sites throughout the world that contain marvelous masonry structures that relate to famous events or people in history. One such site is the Ancient City of Gordion, located in modern-day Turkey, which is approximately 60 miles southwest of Ankara, near the village of Yassihuyuk. Gordion is one of the most important archaeological sites in the Near East, having been occupied for more than 4,000 years.
Gordion was part of the Phrygian Empire and is connected to history from the late 8th century BC and the myth of King Midas. He reportedly starved because his “Midas touch” turned all to gold which also rendered his food inedible so that he starved.
Another story dates to 333 BC. Alexander the Great traveled through the region on his campaign to conquer the Persian Empire. During his stopover in Gordion, he learned about a special wagon in the Temple of Zeus. “The pole of the wagon was tied to the wagon body with an intricate knot of cornel bark, and a prophecy had foretold that whoever could unfasten the knot would go on to rule over Asia (or even the whole settled world, in one version). Seized by a longing to test the prophecy, Alexander tried to unfasten the knot by unraveling it, but when he was unable to do so, he drew his sword and cut right through it. From this comes the proverbial expression “to cut the Gordian Knot,” meaning to cut right to the heart of a matter without wasting time on external details.” (credit: THE GORDIAN KNOT, Digital Gordion, University of Pennsylvania). Cutting the knot, Alexander became the ruler of Phrygia and, subsequently, of all of Persia.
The evolution of the city is interesting as well. The Early Phrygians (9th Century BC) built a stone fortress (citadel) to protect the city. To expand the city, the Middle Phrygians (ca. 800-540 BC) systematically buried the early citadel and built a larger city above it. This begins our story of marvelous masonry concerning the first city and the second city. The first city was the home of Midas, and the second city was the site that Alexander visited. By 189 BC, Gordion was abandoned under pressure by Roman activity. The majority of the second city stone was quarried away, and the buried first city remained forgotten.
In 1893, Gordion was rediscovered by German archeologists, but it was not until 1950 that Rodney Young of the University of Pennsylvania began excavations of the first city. What was uncovered included an Entry Gate complex that is now considered the best-preserved citadel gate in Iron Age Asia Minor. While such a large archeological site has numerous stories to tell, we will discuss the marvelous masonry of the Entry Gate complex and the restoration of the South Court walls.
Figure 1 shows only the gate complex in 2012; it includes the walls of the North and South Court buildings. The ramp area was the citadel entrance, and the interior of the North Court building was excavated, but the South Court building was not. The unexcavated walls of the South Court and the east walls of the North Court are now acting as retaining walls. Remnants of the second city and material used to bury the first city are shown as well.
Figure 1 – Gate Complex, 900 BC
Figure 2 is a rendering of the original Gate Complex. The original walls were estimated to have been approximately 60 feet tall. The red lines indicate the existing walls in Figure 1, which is currently 33 ft tall.
Figure 2 – Gate Complex As Imagined By Archeologists
The photograph in Figure 3(a) was taken after excavation; Figure 3(b) is the north wall of the South Court when the author first viewed the site in 2012.
Figure 3(a) – Gateway After The 1955 Excavation, Viewed From The Southwest (Courtesy Gordion Archive, University of Pennsylvania)
Figure 3(b) – North Wall Of South Court (2012) Viewed From The North
The archeologists also located a unique pebble mosaic pavement that extends throughout the gate ramp. Underneath the pavement is a system of drainage trenches. That may be due to Gordion being very close to an ancient river, and the Phrygians were well-versed in subgrade drainage techniques. Unto itself, the gate ramp represents a significant archeological discovery, and any conservation effort on the walls needs to protect the ramp.
The South Court wall construction is multi-layered, with roughly-coursed facing stones of limestone intermixed with rhyolite; the rubble core is earth and stone rubble. Figure 4 shows the North Court walls (c.1955) viewed from the west with the rubble core visible. The wall thickness varies from 10 to 18 ft; in other wall areas of the Gate Complex, wall thicknesses are as thin as 3 ft. The facing stones vary in depth from 28 to 36 inches and weigh as much as 2600 lb. The walls are battered inward, approximately 6 degrees. The facing stones were set dry with chinking stones; earthen mortar was packed into the surface of the joints and was used as a surface parge coating. The stones were not bedded with the earthen mortar. Reportedly, the parge coating had a lime wash to protect it from weather and provide an aesthetic finish. With the earthen mortar and parge coating, the stone joints would not have been visible on the original walls.
Figure 4 – North Court Walls During 1955 Excavation (Gordion Archive, University of Pennsylvania)
When the walls were exposed by the archeologists, the joints were still packed with earthen mortar, but most of the surface coating was gone. Amazingly, there are still areas where the earthen mortar covers sections of the walls (arrow, Figure 5a). Despite being exposed to the weather for approximately 60 years, the bond of the remaining earthen mortar is still substantial. Most of the walls have eroded joints (Figure 5b).
Figure 5(a) – Earthen Mortar And Coating
Figure 5(b) – Open Joints
In 1986, a bulge occurred in the north wall of the South Court. Archeologists attributed it to joint erosion and freeze-thaw action on the rubble core.
In 1999, Turkey experienced two destructive earthquakes in the northwest, causing widespread damage and the loss of more than 17,000 lives. Although centered nearly 140 miles from Gordion, the earthquakes increased the South Court wall bulge by approximately 1 to 2 inches. Since then, the bulge has continually enlarged to the point where a partial collapse was likely. The bulge extended about 11 ft from the top and the full length (30 ft) of the wall. Portions of the bulge exceeded 8 inches, represented a safety concern for anyone near the wall, and threatened the loss of a major historical artifact (Figure 6). While several of the walls sustained lesser damage, the South Court walls became the primary focus of restoration.
Figure 6 – Bulge Location On The North Wall Of South Court
In Figure 6, the lower portion of the wall shows where previous conservation efforts included grout injection into the wall. Conservators used a lime-based grout in an attempt to fill perceived voids in the rubble fill, but that work was halted in favor of an overall assessment of the wall.
INVESTIGATION AND ANALYSIS
Starting in 2012, visual inspections, measurements, and documentation of the South Court walls and the bulge were performed to assess the condition of the walls. Joints were probed, and surface penetrating radar was used. The inspection results revealed that the facing stones were often cracked and gaps existed behind the facing stones. The gap between the rubble fill and the facing stones even reached a maximum of 5 inches. Moreover, the rubble core material was sampled and tested for density and identified as a dense mixture of limestone, earth, and gypsum.
Based on the data obtained from the inspection and testing, structural analyses of the South Court walls were performed for the assumed original condition and the current conditions. The overall stability of the structure was assessed by taking both global and local failures into account.
When constructed, the South Court walls were approximately 60 ft high exterior building walls with a roof; now, they act as 33 ft retaining walls. The unequal soil condition was created by the sequence and duration of the archeological excavations. Therefore, lateral earth pressure had to be taken into account along with the self-weight of the structure to evaluate the seismic effects.
The assessment had to consider the previous attempts to conserve the walls. Between 2002 to 2006, mason conservators pointed the joints in the lower portion of the wall partial depth with a lime-based mortar, made in-situ repairs to cracked stones using micro-pinning and injection techniques, and injected the perceived voids in the rubble fill using a lime-based grout. The grout used hydraulic lime and lime putty; the mortar used lime putty. The grout was installed using gravity methods. No anchors were placed into the wall. The grout injection program was halted before the entire wall was completed in favor of performing an overall assessment.
After the walls were exposed by the excavations, the tops of the walls and rubble fill were covered in 1956 with an unreinforced concrete cap to limit water penetration into the rubble fill; however, that cap reportedly began to crack immediately. The concrete cap was later replaced in 1988 (Figure 7a). Cracks in the cap were sealed in 1996.
The concrete cap was only effective until it cracked. After that, water infiltration concentrated into the wall at the cracks themselves. Water penetration led to the initial development of the facing stone bulge that was first observed in 1986. Conservators subsequently developed a soft capping method that included a waterproofing membrane covered by natural grasses and plants (Figure 7b). The grassy portion has weep tubes to drain. However, the South Court walls with the bulge never received the soft capping conversion.
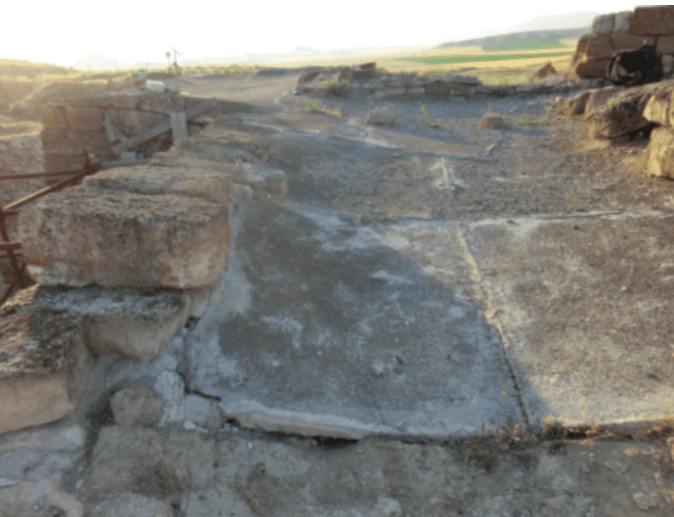
Figure 7(a) – Concrete Cap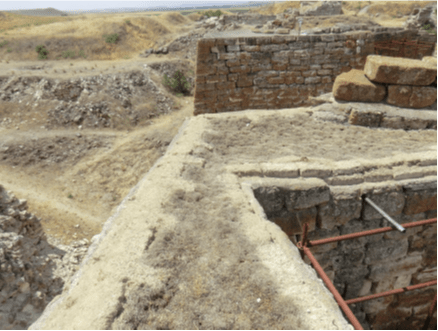
Figure 7(b) – Soft Capping On North Court Walls
Some results identified were:
- The unexcavated court walls are susceptible to damage during a maximum design earthquake.
- The court walls are not internally stable in the static condition unless the internal rubble fill acts compositely with the facing stones.
- The court walls are not internally stable because the facing stones in the bulged area of the court walls are not working compositely with the internal rubble fill.
- The facing stones of the bulge need to be rebuilt with anchors into the rubble fill.
- The capping of the South Courts walls was not adequate; water infiltration was still adding to the facing stone deterioration.
The assessment determined that the bulge was too unstable and that previous work of only injecting the rubble fill and repointing the walls was not sufficient to conserve the wall. The decision was made with the approval of the Turkish government to remove and rebuild the bulge and anchor the facing stones. No attempt was to be made to restore the walls’ earthen surface coating. Therefore, pointing the joints was allowed to limit water infiltration.
Plans and details were prepared and submitted to Turkish authorities. All funding was provided by private sources obtained by the University of Pennsylvania, but Turkish approval, scheduling, and oversight were mandatory.
The restoration/conservation had two key ingredients:
- Restore and conserve the South Court walls. Rebuild and repair the damaged north walls and repair the east walls.
- Protect the historically significant pebble mosaic pavement of the ramp.
Now the reality of the work conditions must be addressed:
- The work will be performed in a very rural area. The closest major city for supplies is 60 miles away.
- The availability of heavy lifting equipment is limited and costly (operator, mechanic, and fuel).
- There are few restoration masons available but many willing Turkish laborers.
- Archeologists mostly work with conservators, not building contractors.
- The work site is only available for approximately 8-10 weeks per summer. Most archeologists are academics and only available during summer break, and the Turkish authorities wanted to limit staff time at the site. Therefore, the work had to be performed over several years.
REMOVAL AND STONE CONSERVATION
To address access to the wall and moving stones, it was decided to purchase an aluminum German-made scaffolding system and gantry hoist that would allow all stones to be moved with manual labor. While expensive, the system would have a resale value to recoup much of the initial investment.
To avoid lowering all the stones to grade, the author designed the scaffolding to support the gantry and provide a 240-pound-per-square capacity on the upper two levels. The gantry hoist had a 3300 lb. lift capacity. With these loadings, the scaffolding system imposed significant leg loads on the foundations. To avoid damage to the pebble-mosaic pavement, a foundation system was developed for the scaffolding (Figure 8a). It included a 12-inch compacted layer of earth to provide a base for a grid of used railroad ties that were loaned to the site for the work. The ties were used to distribute the scaffold leg loads and prevent crushing the subsurface drainage.
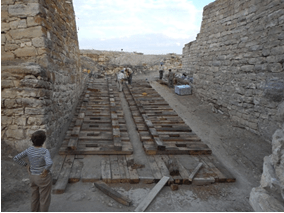
Figure 8(a) – Earth Mat Foundation And Railroad Ties 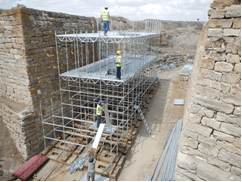
Figure 8(b) – Scaffold Erection
The gantry system would facilitate the removal of the facing stones using only manual power. Figure 9 shows a stone being moved. Each stone was individually assessed and placed on the upper level of the scaffolding or lowered to either the next level or mat foundation for conservation treatment or storage.
Figure 9 – Gantry In Operation
The work crew included conservation masons from Italy and Turkish laborers who adapted quickly to the stonework and functioned like masons. The Italian team had been working on other projects on-site for several years, was very familiar with working conditions, and introduced good restoration techniques and materials. Most of the Turkish workers had full-time jobs that they left for the summer work season because it paid more. One was a shepherd who hired another to tend his sheep while he worked, earning less than $1.00 per hour.
Work was performed starting at 6 am and was stopped at 12:30 pm due to excessive heat. Working in the sun around the stones, temperatures regularly reached or exceeded 100°F. Hard hats were provided but rarely used. Besides hats and sunglasses, the primary protection was gloves and steel-toed shoes. Materials that weren’t readily available in Ankara were shipped in on short notice from Italy and Germany.
The Italian supervisors could communicate in English and Turkish. The Turkish supervisor understood some English. At the start of the construction, a Turkish colleague and former student of the author, Semih Gonen), was hired to be on-site full-time and greatly improved communications. He also implemented other design projects on-site. The author was on-site 2-3 weeks a summer and available by internet.
Damaged stones were conserved by epoxy pinning the stones together (Figures 10a and 10b). Before this project, the pinning technique and materials (epoxy and stainless-steel threaded rods) were developed and used by conservators on stones from other walls for approximately eight years; the techniques were accepted by Turkish authorities. In the US, preservation standards have accepted epoxy for limited uses without addressing the anticipated longevity.
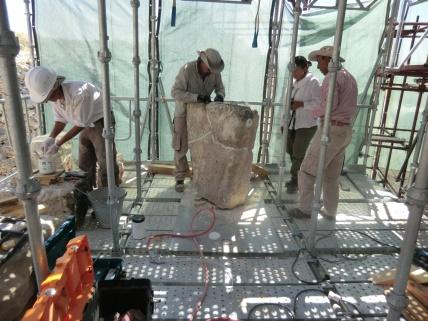
Figure 10(a) – Stone Conservation 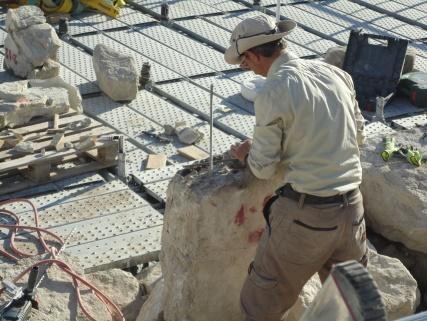
Figure 10(b) – Stone Conservation
RUBBLE EXCAVATION AND CONCRETE CAPPING STABILIZATION
Upon removal of the concrete cap and facing stones, the condition of the facing stone and fill was confirmed. The fill behind the separation was densely compacted (Figure 11) with little erosion. Confirming the assessment, it was apparent the bulge of the facing stones was due mainly to displacement of the facing stones from the fill as well as damage to individual stones. There was very little keying of the facing stones into the fill. The smaller stones behind the facing stones acted like a break with the fill.
Figure 11 – Damaged Facing Stones, Compact Rubble Fill, And Void Behind The Facing Stones (Photo: Elisa Bono, 2015)
As the facing stones were removed, the fill was also excavated to prevent sloughing. Figure 12 shows the temporary protection being placed to protect the concrete capping from being undermined as the fill was excavated. Keeping the capping intact was essential because it also supported the gantry.
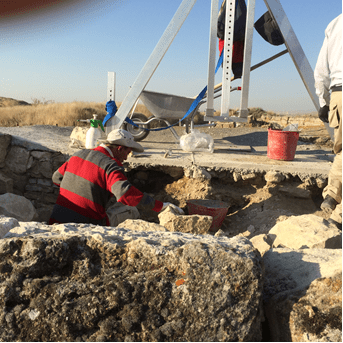
Figure 12(a) – Capping Support Being Placed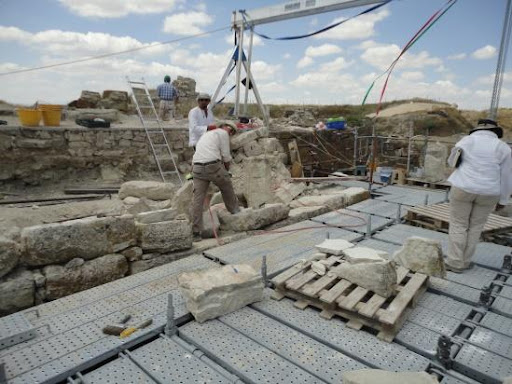
Figure 12(b) – Capping Protection Visible Beyond
FACING STONE INSTALLATION AND WALL STRENGTHENING
The localized strengthening of the facing stones was achieved by anchoring the stones into the fill using mechanically-stabilized earth techniques. Stainless steel straps (3/8 inch x 2-inch wide x 8 ft long) were attached to the stone with a 3/8-inch stainless steel bolt (Figure 13) and embedded into the fill that was grouted (Figure 14). Additional vertical rods were grouted into the fill (Figure 15).
Each stone (original or repaired) was installed in its original position (Figure 16).
Strap anchors were placed every other course on every stone (Figure 17). Corners were interlocked with strap anchors also (Figure 18). Stones were set in mortar and the joints pointed.
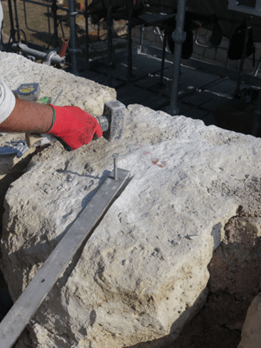
Figure 13 – Anchored Facing Stones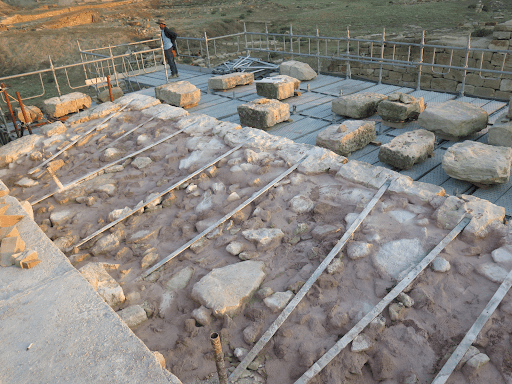
Figure 14 – Fill Grouted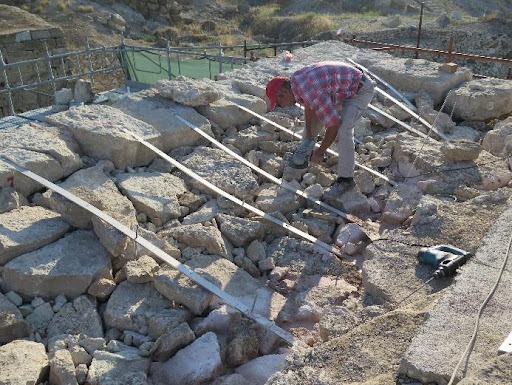
Figure 15 – Straps With Vertical Rods To Be Grouted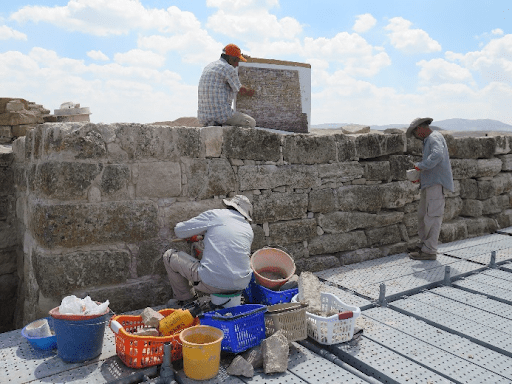
Figure 16 – Stones Installed In Their Original Locations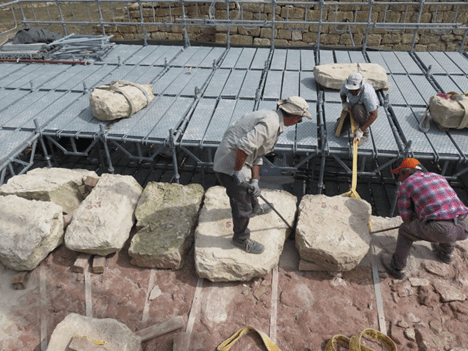
Figure 17 – Alternate Stone Courses Anchored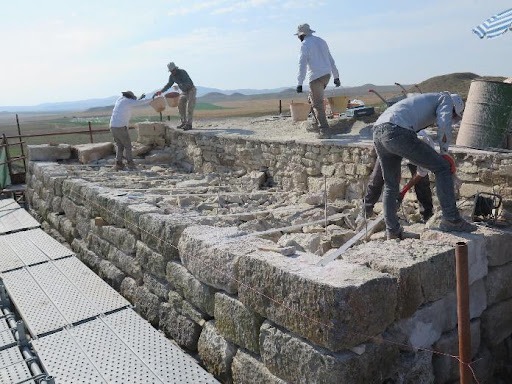
Figure 18 – Corners with Straps
To complete the last few courses in the time available, a crane was brought in (Figure 19).
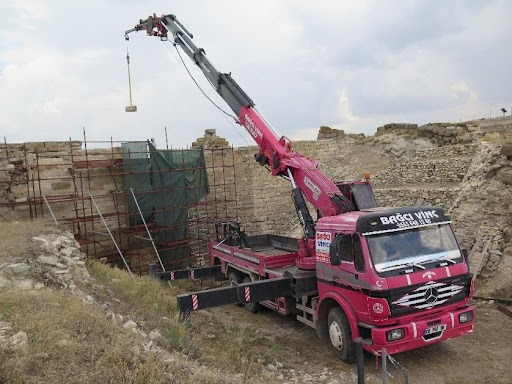
Figure 19(a) – Crane For Final Courses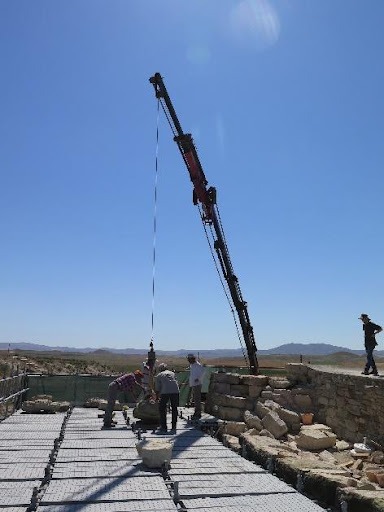
Figure 19(b) - Crane
IN-SITU REPAIRS
Portions of the South Court walls that were not rebuilt (north and east walls) were conserved in place. Figure 20 shows pinning. Figure 21 shows grouting minor voids. The grout formulation was determined on-site using a sample wall; it was lime-based. Voids were determined by probing open joints. Figure 22 shows stone replacement. Figure 23 shows adding stone chinking before repointing. Originally, the chinking filled the gaps between the facing stones, minimized point loading from the wall above, and reduced the amount of earthen mortar to fill the surface of the joints.
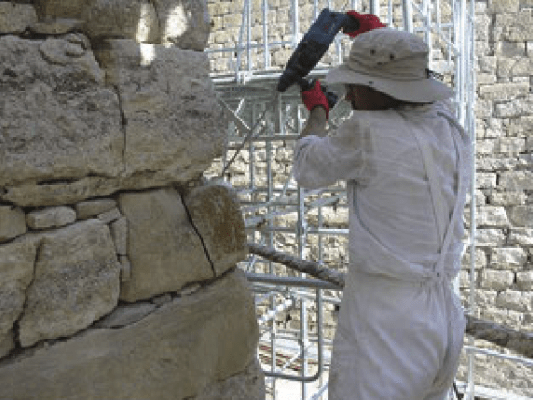
Figure 20 – Pinning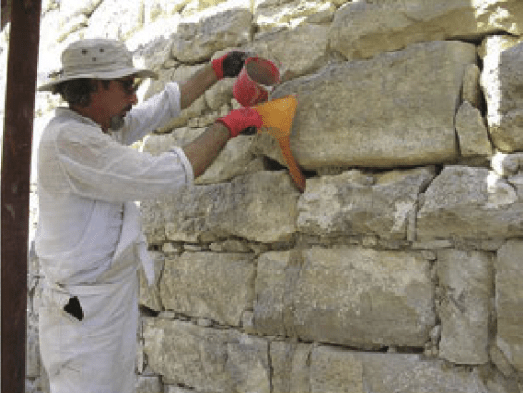
Figure 21 – In-situ Grouting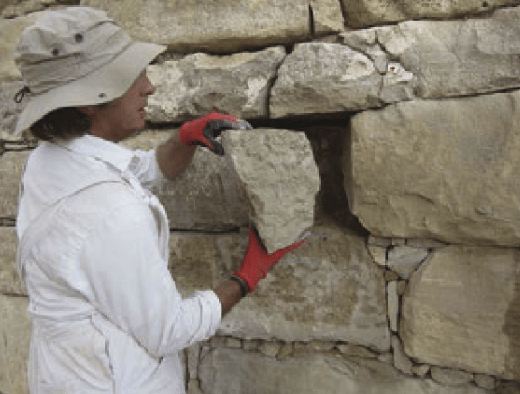
Figure 22 – Stone Replacement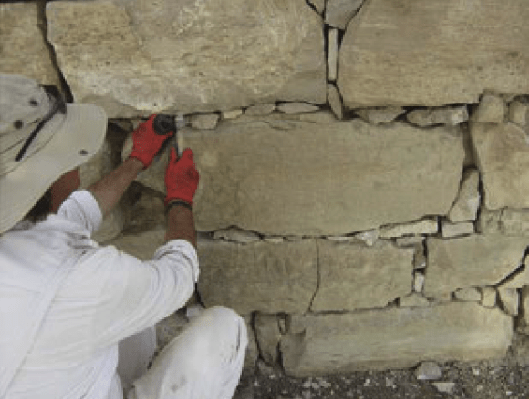
Figure 23 – Chinking Joints
COMPLETION
Figure 24 shows the completed project. The scaffolding and mat foundation system was removed, and the site was seeded with historically natural grasses.
Figure 24 – The Completed Restoration
Figure 25 shows the east wall of the South Court. This wall was restored in-situ without rebuilding. The softcap was also added to protect the top of the walls from future water infiltration.
Figure 25 – East Wall After Further Excavation And Wall Repairs
Going forward, the walls are to be monitored for cracks and movement. A future assessment will be made as to whether to anchor the facing stones in the 2002-2006 grouted area. Finally, approximately 1/3 the height of the backfill behind the South Court walls will be removed to improve the global stability of the walls. Any facing stones exposed by that removal will have to be conserved and pointed, similar to what was done on the east walls.
While only the work at the Entry Gate was described, several other notable projects were completed in the city. For anyone traveling through Turkey, it is worth a visit to Gordion! The sites are spectacular, and the people are wonderful!
SUMMARY
The assessment and conservation of one of the most significant historical masonry cities, dating to 950 BC, was described. The Early Phrygian gate complex initially survived until 1953 by having been systematically buried. Following archeological excavations, the walls then began a second phase of deterioration due to environmental effects and seismic activity. The recent conservation effort to protect the South Court walls was described. The rebuilding of a significant bulge in the facing stones required anchoring and strengthening. The details and process for evaluation used on the South Court walls can be used to assess and restore other Gordion walls.
Hopefully, this wonderful example of Marvelous Masonry will survive another 3,000 years. Working on such a magnificent masonry structure has been an honor and a privilege!
ACKNOWLEDGMENTS
Restoration design by David Biggs, Biggs Consulting Engineering, Saratoga Springs, NY. Additional site design and Site Restoration Engineer, Semih Gonen, Ph.D.
The author wishes to recognize C. Brian Rose, Director, Gordion Archaeological Project, University of Pennsylvania; Elisa Del Bono, Field Director, Aysem Kilinc-Unlu, Architectural Conservator; Frank E. Matero, Professor, School of Design, Historic Preservation, University of Pennsylvania,
The Gordion project receives generous support from the University of Pennsylvania Museum of Archaeology and Anthropology, the C.K. Williams II Foundation, the Selz Foundation, the Loeb Classical Library Foundation, the Luther Replogle Foundation, the Merops Foundation, the J. M. Kaplan Fund, and the Jordan Foundation. In particular, we thank the Turkish Ministry of Culture and Tourism and the Museum of Anatolian Civilizations in Ankara.