Anchoring with Thermal Efficiency in Mind
Words: Linda Potter
Words and Photos: Linda Potter, CSI, CDT; Manager of Architectural Services, Hohmann & Barnard
Times are changing in masonry. We aren’t building in the same manner we were 25 years ago or even 5 years ago. What that means for the mason contractor is that we have to build buildings differently, if we expect them to perform differently.
We now look at masonry walls as systems. The architect needs to consider every component inside a wall assembly and how it impacts the adjacent material. Compatibility of materials, penetrations, thermal bridging, and vapor permeability are important. These wall assemblies are now sophisticated building envelopes, not just brick walls, which means there isn’t a one-size-fits-all approach for anchoring.
Every project has the potential to need a different anchor based on wall assemblies, building codes, LEED requirements, passive house strategy, etc. You need to know what the owner/architect’s goal is for the performance of the project in order to protect yourself by including in your bid the appropriate accessories.
Impact of Anchors on Thermal Bridging
A stainless steel anchor has one-third the thermal conductivity of carbon steel and one-seventh the thermal conductivity of zinc. Switching to stainless steel anchors is one way to impact the thermal performance of an anchor.
Stainless-steel barrels have 1/3 the thermal conductivity of carbon steel barrels and 1/7 the thermal conductivity of the zinc barrels of our competitors’ products.
Hohmann & Barnard partnered with a leading firm in thermal engineering several years ago to quantify the impact anchors have on a building with a series of tests. We took our best performing anchor at the time – the 2-SealTM Tie – which is a single-penetration zinc anchor, and tested it with 1”, 2”, 3”, and 4” of insulation and at different spacing requirements from 8” to 24” to find out how those small, but numerous, thermal bridges were impacting the design intent.
The results confirmed our suspicion. At 8” spacing with 4” of insulation, the R Value of the wall assembly was reduced by 30%. If we look at 16” spacing and 2” of insulation, which is more commonly used, we end up with a 13% R Value reduction. Keep in mind, this is with a single-penetration barrel anchor. The more fasteners or prongs that are penetrating the insulation, the worse those values will be. Current building code does not recognize brick ties as thermal bridges that need considered in R Value analysis, but the day is coming when it will.
H&B switched out the zinc barrel for a stainless steel barrel. We put a UL 94 coating around the barrel as a thermal break and re-tested with the same variables. This time, we ended up with 93% thermal efficiency for 16” vertical spacing and launched the Thermal 2-SealTM anchors into the market.
Addressing the thermal bridging aspect of thermal performance is only one part of the equation, when we consider an anchor that is suitable for a wall assembly. Air barriers are critical to a thermally efficient building design. If a penetration is made to an air barrier, there must be a plan for controlling air leakage. You can utilize gasket tape with standard anchors, but it’s one more step that includes more time. If we want these buildings to perform differently, we can’t ignore this critical part of air barrier installation. The Thermal 2-SealTM anchor line includes two EPDM washers to seal both the face of the insulation as well as the air/vapor barrier.
This is an example of a thermally broken, single-penetration barrel anchor that seals at the insulation and air barrier interface.
Continuous insulation is an important consideration when selecting an anchor for a wall assembly. We see a lot of rigid and mineral wool used in wall assemblies. With previous iterations of anchors, the backplate anchor was attached to the sheathing/stud, and then the insulation was fit in between the courses of anchors. It’s more expensive to buy strips of 16” insulation and its installation time compared to a full sheet must be considered.
For the application of H&B’s barrel anchor, full sheets of insulation can be used with anchors post-installed into the stud, sealing at each penetration to control air leakage with the added feature of the wingnut to tighten the insulation up tight against the backup, removing the loss of R Value from displaced insulation. If the insulation needs to be mechanically fastened to the backup, this anchor can serve as the insulation fastener, reducing the amount of penetrations through the air barrier and insulation. This further improves the thermal efficiency of the wall assembly.
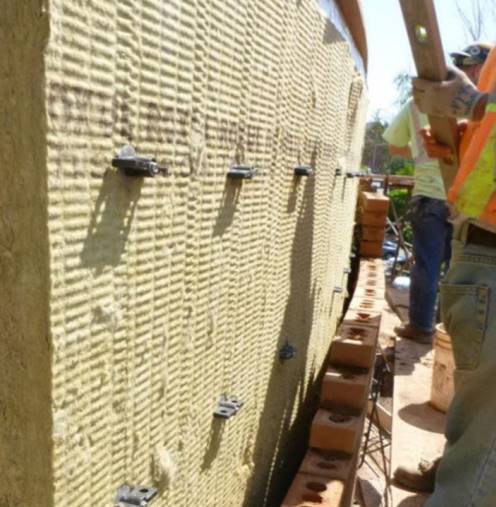
Shown here is a barrel anchor – H&B’s 2-SealTM Thermal Wing Nut anchor – used in conjunction with mineral wool, acting as the insulation fastener and the brick tie
Integrated joint reinforcement and anchoring systems have been used for many years, and while it is still widely used, some design professionals are moving away from these hook-and-eye systems into the post-installed thermal anchors for one large reason: The eyelet protruding from the CMU is a common problem when it comes to air barrier detailing.
In many cases, each eyelet needs to be detailed prior to the air barrier installation to pass air leakage tests. The time and money for detailing properly cannot be ignored. The cost of a thermal anchor with the EPDM washers that seal at the air barrier penetration to a standard anchor is not equal. Using post-installed thermal anchors results in a ROI.
The learning curve with post-installed thermal anchors is short. Mark the studs before the insulation goes on, so you know where to place the anchors. Order the correct size that fits the wall makeup, so the two seals line up with the insulation and air barrier interfaces. Wall assemblies vary from project to project, which means you likely can’t stock these anchors and will need to plan for lead times and delivery to the project.
The last thing to note is that some backups will require pre-drilling, especially high PSI concrete backup. The best thing you can do is get some of these thermal anchors in your shop. Embrace this innovation as a way to keep masonry relevant and moving forward with evolution of building codes and thermal efficient building performance.