Critical Root-Cause Analysis (Part Two)
Words: Zach Everett
CLICK HERE TO READ CRITICAL ROOT-CAUSE ANALYSIS (PART ONE)
Words: Zach Everett, Brazos Masonry Corporate Safety Director
Photos: marekuliasz
Critical Root-Cause Analysis And Its Purpose
The safety of workers is nothing new. The Bible reads, "When you build a new house, then you shall make a parapet for your roof, that you may not bring guilt or bloodshed on your household if anyone falls from it” (Deuteronomy 22:8, NKJV).
God was concerned about safety. Even physically. He did not want people falling off roofs and dying or being maimed. Roofs were places to gather together, work, bathe, and more. So, particular care was to be put into protecting against the hazards associated. Millennia ago, safety was a concern, but history shows we have had our low points in safety as well. It has only been in relatively recent years that we have seen such a heightened focus on safety in the industrialized countries. It hasn’t been too long ago that fatalities in building bridges or buildings was just “a cost of doing business.” Losing fingers or whole limbs in shop work was just a hazard of the job. In the 1930s it was figured that there would be one construction fatality for each $1 million in cost. 28 lives were lost building the San Francisco Oakland Bay Bridge. The Golden Gate Bridge was considered a safety marvel with “only” 11 fatalities. The Brooklyn Bridge fatality numbers vary. The project took 14 years to complete and no one person was responsible for records. The lowest count was at 21; the highest 40. The Hoover Dam construction officially had 96 deaths… officially. Some contend it was much higher.
Today those injuries are considered unacceptable. It is not merely “a cost of doing business.'' We will go to great lengths to prevent those injuries, but we must first figure out how and why they happened. What string of events took place that led to the incident? This is where the critical root-cause analysis was born. If we can drill down, find out exactly what events caused the incident, and remove those steps… the incident will never happen. There are many strategies and techniques of how to conduct a root-cause analysis. There is the Bow Tie method, the Fish Bone method, and Fault Tree analysis, which are ways to outline and diagram the events. There are root-cause analysis software that is supposed to help you find the root-cause of the incident after you input all the details, such as TapRoot and others. I would like to focus on one that is one of the more simplistic, but effective root-cause analysis methods. It is called the “Five Whys'' method.
Asking The "Five Whys"
Sakichi Toyoda is credited for the development of the “Five Whys” technique of root-cause analysis for the Toyota factories. It’s simple, but powerful. We continue to ask why just like a young curious child continues to ask consecutive “whys” of his parents about the sky, bulldozers, giraffes, tacos, body hair, and 1000 other things. This is our natural way of learning. As adults we should continue to learn, especially in matters as important as our workers' lives. In the “Five Whys” technique, we ask why a particular problem or event happened, when we reach that answer we ask why did that particular event happen, which led to the final event, and so on. Eventually we drill down to find the root cause. This process of asking why repeatedly does not only find the original root cause, but also gives a window into the chain of events or process that led to the problem or incident. This is highly beneficial when applying this methodology to problems in finances, equipment ware, relationships, or anything. It shows us where we got off the rails. It shows us the escalation of tempers, missed maintenance, or communication is breaking down. Recognizing these patterns reveals the secret to avoiding the same catastrophes in the future.
The number five in the Five Whys method is not magical. There is no real significance to the number five. It is simply a rule of thumb that, in most cases, gets you down to the root of most problems. There are incidents that are born out of such a complex process that five “whys” are not near enough to outline the events that led up to the final incident. This is the case with the Space Shuttle Challenger tragedy that we began with. There were too many moving parts, pieces, people, processes, and problems to chart this catastrophe adequately in just five steps. Following I have gone ahead and created a Five Whys flow chart to outline the Challenger chain of events leading back to the root-cause, just for a simplistic example of the analysis process. For this example, I stuck with the rule of thumb of only five “whys”, however in a tragedy of such complexity, there could be hundreds of “whys” and additional “legs” of the flow chart as some answers can lead in different directions.
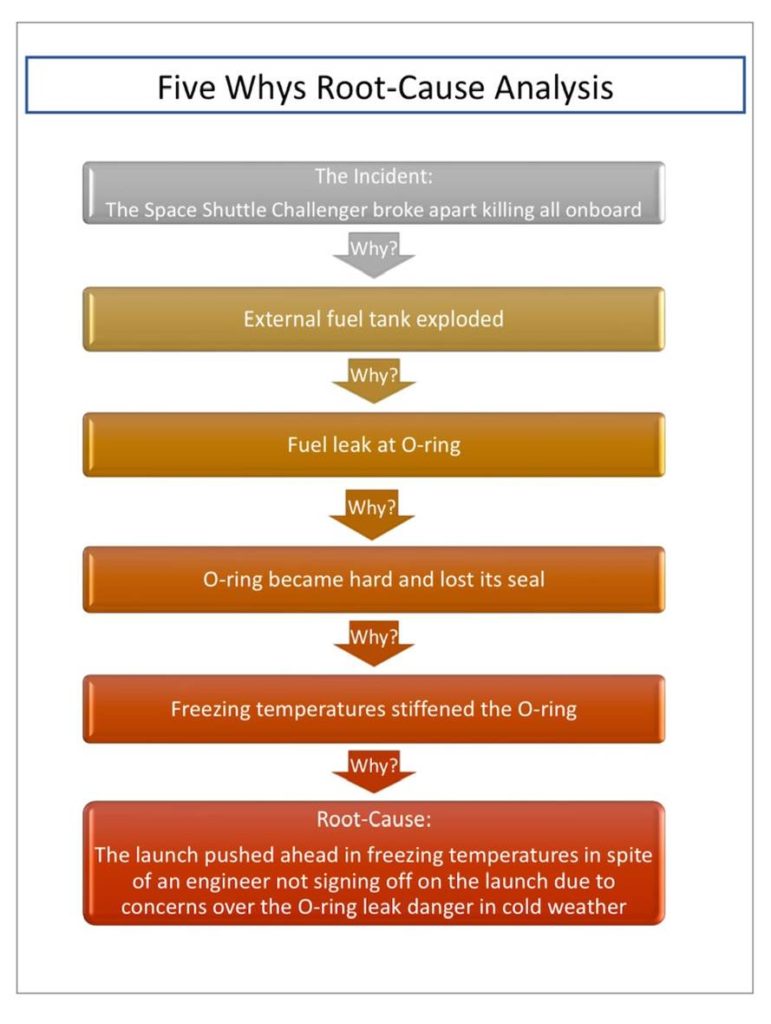
As you can see in the Five Whys flow chart on the Space Shuttle Challenger, it shows quickly and clearly the faulty chain of events that led to the deaths of these special people. Again, this is an utterly simplistic view, knowing there is far more at play, but if they would have just postponed the launch… the history of this mission could have been a successful one.
With each incident we experience, we too can learn to avoid the same types of incidents in the future. As they say, “If we don’t learn from the mistakes from history, we are doomed to repeat them.”