Staying Safe on the Jobsite
Words: Dan Kamys
Safety
By K.K. Snyder
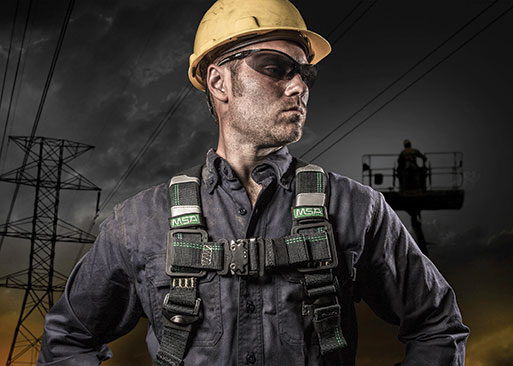
It’s no secret that masonry construction is physically demanding and has a high risk of work-related injuries. According to the latest report of the Bureau of Labor Statistics, masonry construction is recognized as one of the high-risk specialty trades, with the nonfatal incident rate of 191.5 per 10,000 equivalent full-time workers and 2,640 recordable injuries.
Jobsite safety is an ongoing concern for contractors who have the overall responsibility to keep employees from being injured or even killed. Additionally, injuries can mean a shortage of available workers and a potential increase in the financial bottom line.
So what are the main safety concerns on a masonry jobsite, and how can contractors and supervisors get their employees to understand and adhere to the various rules and regulations, from wearing correct personal protection equipment to proper use of scaffolding? Utilizing myriad training resources available in the industry and refusing to accept shortcuts when it comes to safety are paramount steps toward safety. Shortcuts that can potentially end in tragedy.
From the top
The Occupational Safety and Health Administration (OSHA) is responsible for the administration and interpretation of issues related to record keeping and safety standards. Casey Perkins, OSHA area director for Austin, offered some insight to what inspectors are looking for when they visit a jobsite.
He says the administration’s “focus four hazards” targets potential construction hazards that send up red flags for inspectors. On the masonry jobsite, those include fall protection, electrocution hazards, “struck by” (meaning struck by heavy equipment or falling materials), and “caught-in” or “caught-between” with regard to equipment hazards.
Falls from roofs, open-sided floors, scaffolds and ladders are the leading causes of serious and fatal injuries in residential construction. OSHA’s safety requirements for fall protection are clear cut.
“In general, fall protection starts at six feet high for things like exposed ledges or balconies, but the scaffolding requirements start at 10 feet high,” Perkins says.
Other considerations for scaffolding safety include having the equipment fully planked, keeping it in good repair, using guardrails and personal fall arrest systems if working above 10 feet high, and keeping footings of the scaffold on a solid surface, rather than on stacked bricks or piled lumber.
“Masons are good about using a welded-frame scaffold, designed and made by a qualified manufacturer for that purpose, as opposed to scaffolding being made at the jobsite with no load ratings or design criteria,” he says.
In addition, when scaffolding goes higher than the 4:1 height-to-base ratio, it must be restrained from tipping by guying, tying, bracing or an equivalent means.
“Failed scaffold and job-built, man-baskets often fall from their supports and have tragic consequences for workers,” Perkins says. “In recent years the Austin area has seen its share of these fatality cases. Employers need to ensure the proper equipment for working at heights is supplied to the workers.”
Electrocution hazards on the masonry jobsite are vast, though many are the same as hazards on any construction site. For masons, working in an outdoor environment where rain and moisture are present is unavoidable. To prevent electrocution, a ground fault circuit interrupter should be used, says Perkins. In addition, because cords typically are stretched out across the jobsite, it’s important to protect cords from foot traffic, forklifts and other heavy equipment.
Masons are especially susceptible to being struck by a piece of heavy equipment or falling materials. Wearing hard hats and safety glasses, and having toe boards on scaffolding to prevent buckets, tools and bricks from being kicked off, are safety essentials.
Being caught in or between equipment includes faulty practices such as removing the hatch guard from the top of a mud or cement mixer.
“We sometimes find that missing (during an inspection),” says Perkins. “They need to leave the guard in place so no one gets their hand in there.”
With the guard missing, items such as pencils or tools can fall in, prompting a worker to try to quickly reach in to retrieve it. This is an accident just waiting to happen.
It stands to reason that the safety requirements most common to masonry jobsites also are those most often found violated, with fall protection and scaffolding violations, by far, the most frequent, specifically the lack of guard rails and failure to fully plank. “If it’s a five-foot-wide scaffold, they need to plank the entire five feet, not just use one or two planks,” says Perkins.
Zach Everett, corporate safety director for Brazos Masonry Inc. in Waco, Texas, chairs the Mason Contractors Association of America’s (MCAA) Safety Committee. MCAA’s latest focus has been working with OSHA on a new silica exposure standard, which OSHA estimates will save nearly 700 lives and prevent 1,600 new cases of silicosis per year, once the full effects of the rule are realized. Currently still under review, the proposed rule has gone through public hearings already.
“There are a few things we’d like to see in the standard,” says Everett of the MCAA’s input regarding the silica rule.
In addition to the dangers already addressed, heat illness prevention is also a masonry jobsite concern and is addressed by OSHA’s “Water. Rest. Shade.” campaign.
“They’ve got to make sure that folks are getting proper time to rest, that they seek shade during that rest, and that they get proper hydration,” he says.
Having material safety data sheets and eye wash on the jobsite, and using protective eyewear, are essential when completing tasks such as washing down bricks with muriatic acid.
When it comes to complaints, Perkins says, OSHA doesn’t receive many from workers on masonry sites. Instead, the majority of complaints come from the general public concerned for their own safety or reporting a nuisance issue, such as dust created from cutting bricks and blocks. “Potential falls are, by far, the most common complaint or referral,” he says.
In addition to calls from the public, violations often are called in by compliance officers who just happen to see a violation while driving by on the way home or on the way to another inspection site. In that situation, the officer would stop and initiate an inspection.
OSHA rarely announces a planned inspection prior to arrival, though exceptions exist in severe situations, Perkins says. If time and travel for an officer to arrive at the worksite is an issue, for example, an inspection might be opened by phone, so the situation can be immediately addressed.
Based on a priority system, OSHA warrants site inspections in cases of imminent danger, fatality, catastrophe (defined as three or more being hospitalized due to an event), or receipt of a complaint or referral regarding a violation. Planned visits targeting various OSHA programs are other reasons for a site inspection. In that case, some research may be done to create a list of all masonry businesses in a certain area, for instance, with a few being selected for inspections.
Perkins says being proactive, rather than reactive, to an OSHA site visit is key. “Refer to our website and to your local officers. Reach out and ask questions to get our perspective on available corrective actions,” he says. “OSHA always wants employers to have a ‘find it and fix it’ self-inspection program, encouraging supervisors and employees to report things that are a concern to them, even if they didn’t result in a fall or injury; maybe it’s a tool malfunction that could result in an accident in the future.”
OSHA offers 10- and 30-hour jobsite safety training courses in English and Spanish. The administration also makes available, at no cost, laminated quick cards in English and Spanish on subjects such as scaffolding, fall prevention, and use of personal protective equipment.
“Also, the Construction Industry Digest is a guidebook that condenses all rules into plain language and is a handy reference to keep on hand or just throw up on the dash in the truck,” says Perkins. OSHA provides the booklet in English and Spanish as well.
Selling safety
Marc Harkins serves as product group manager of fall protection products for Pennsylvania-based MSA Safety and says all of their products meet or exceed OSHA requirements for sale in the United States. The company has been in the safety equipment business for 100 years and offers a complete fall protection system, including full-body harnesses, connecting devices and anchorage connectors.
In addition, MSA offers products to protect the eyes, face, head and hearing. While the products marketed are essential to safety on the masonry jobsite, a tremendous value lies in the training classes they offer, from a basic trailer demo to a lunch-and-learn format, says Harkins.
MSA’s construction sales managers have mobile training units – trailers – that can be brought to a jobsite on request for product demos. Using a 220-pound torso, the sales manager can demonstrate what happens to a person during a fall and how the equipment will work. “Participants can see how using the wrong product can cause violent forces in a fall event as well as how using the appropriate product can best protect workers in a fall event,” Harkins says.
More in-depth training classes also are available, such as Authorized or Competent Person for Safety at Heights, as well as Competent Person for Inspection to teach masons how to self-inspect their safety equipment. Training classes are OSHA approved.
In addition to the fall protection systems, MSA Safety offers hard hats with full and front brim, clear visors, chin protectors, sun shades for the back of the neck, ear muffs for hearing protection and eyewear rated for safety use indoors and out.
“We can logo the equipment upon request with their company logo,” Harkins says. “The majority of our hardhat sales are logoed.”
Tops in training
Combining essential training with equipment they manufacture and sell is just good business for Premier Scaffold Solutions and TNT Equipment. While Premier manufactures and sells scaffolding and mast climbing systems, TNT is a rental house with more than 200 rental machines in its fleet.
Before operating, installing or dismantling a Premier mast climber, users must complete a certified training course, ensuring they understand and are confident in their abilities to install, operate and maneuver Premier products around a jobsite. Each certification remains valid for three years.
Since the inception of the company 30 years ago, that policy has served the business well. Michael Solomon, national sales manager for both companies, says the equipment and their training programs still go hand in hand. The No. 1 reason for accidents, especially falls, has also remained the same – complacency.
“In my training classes, I tell them that you can die from a one-foot fall,” says Solomon. “Complacency kills.”
The company offers three levels of training, some on the worksite and some in the classroom, targeting operators, installers and those who will return to the jobsite to train their own employees. For customers purchasing a mast climber, for example, the company sends a rep to help erect the climber, conducting a one-day, hands-on training in the field and a half-day program in an onsite mobile classroom.
“If a general contractor is renting the mast climber from TNT Equipment, we might go back several times to train in operating and accessing, whether accessing from the ground level, from inside a building, or by climbing up with a harness system,” says Solomon, whose three-day “Train the Trainer” classes, typically held at Ohio or Florida facilities, prepare qualified candidates to teach others.
“It covers everything twofold,” he says. “This person will then be able to train their own employees, rather than being at the mercy of waiting for training classes to be conducted.”
Solomon recognizes that even seasoned professionals can make mistakes. That knowledge recently struck close to home when he suffered severe injuries to his arm, a broken nose, concussion, and multiple sprains and abrasions from falling off a new piece of equipment in his own yard.
“It’s brought a new perspective in my desire to be stronger with safety and safety training,” he says of his role to teach others. “It can happen in a flash, no matter how long you’ve been doing it. And, once again, complacency kills.”
Proactive prevention
Whether your job is to enforce safety regulations or just adhere to them, there’s always room for improvement. Brazos Masonry Inc. has high standards for the 200 – give or take – masons the company employs at any given time. To that end, Brazos’ safety policies – part of the intensive Corporate Safety Program – exceed OSHA minimum standards. Going the extra mile can pay off when dealing with OSHA, says Zach Everett, the company’s corporate safety director.
Since joining the company in 2001, Everett has developed and executed safety training manuals and seminars related to scaffold erection, scaffold competent personnel, forklift operation, aerial lift operation, and accident investigation, among others. He says being prepared before a compliance officer shows up for an unannounced inspection is key.
“Being OSHA compliant is great, but there is so much more to safety. If [a compliance officer] comes up and sees that you’re going the extra mile, that’s going to go a long way with them,” says Everett.
Brazos provides its employees with safety training on several levels of intensity in a number of subject areas, beginning with a basic safety program during new-hire orientation. From there, the training depends on what tasks the employee will be performing on the jobsite, from working on scaffolds to operating aerial lifts.
Keeping employees accountable for their own safety is important for a company’s bottom line. While Brazos used to reward employees for clean safety records, Everett says OSHA has discouraged companies from that practice, citing an added pressure for employees not to report incidents. “There is a little bit of merit to what (OSHA) is doing,” he says. “We still offer some incentives, but not based on their injury records.”
Masonry businesses need to have some form of disciplinary plan in place to address infractions. “As hard as you try, you’re going to have some people that are rebellious,” he says. Disciplinary action can range from requiring retraining to sending a worker home without pay or terminating employment.
“We have a couple of things that we allow zero tolerance on, and that’s fall protection and eye protection,” Everett says. “We can’t keep giving them grace on those.”
A great deal of importance lies in supervisor training, says Everett, noting that a disconnect can exist between training the administrators and getting that training to stick in the field.
“Sometimes you see it’s gotten lost between the field supervisors and the guys doing the work in the field,” he says. “If there’s a breakdown in the field supervisor’s motivation, you’ll see more problems.”
At the end of the day, it isn’t just about training but, rather, getting supervisors to convey concern about employees. “They have to get the message across that they value their employees and want to keep them safe so they can go home to their families at night,” Everett says.
K.K. Snyder is a freelance writer based in Albany, Ga.
Return to Table of Contents