Masonry Veneer Installation
Words: Dan Kamys
Case Study: Masonry Veneer
By Ron Treister
Cladding the exterior of buildings with full-cavity-wall type brick veneer fa??ade systems has been an accepted, traditional construction process for centuries. Like any other time-tested building procedure, however, it does have its shortcomings.
As a result, there was a call for something new and innovative to be used as an alternative. And that "something" was direct-adhered, barrier-wall type masonry veneer facades.
The popularity of direct-adhered masonry veneer facades was almost immediate, but there unquestionably was another industry need. That was, a need for a proven technology that would provide permanent, high-strength, direct-to-building installations that also would be freeze-thaw stable, protecting the building from water intrusion.
After more than five decades of re-writing the book relative to the best ways of installing ceramic tile and natural stone via a "system approach," following an extensive R&D program, LATICRETE (Laticrete) stepped into this new arena with its Masonry Veneer Installation System (MVIS). The system brought solutions for the installation of direct-adhered masonry veneers, along with warranties for standing 100 percent behind any installation.
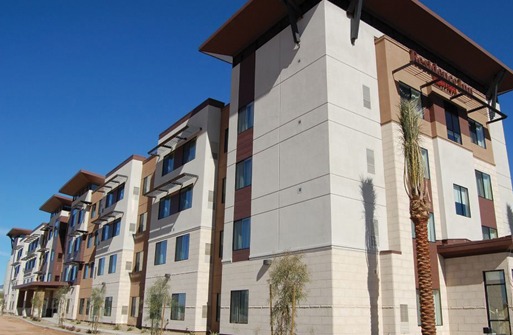
Residence Inn Project
Fast-forward to the Residence Inn by Marriott in Gilbert, Ariz. The project involved 36,500 square feet of exterior cladding. After comprehensive planning sessions, the product chosen to be used as the finish fa??ade material was ARRIS??tile Renaissance, a calcium silicate recreation of natural limestone that maintains the look of full-bed stone installations with the benefits of thin-clad systems.
From a green aspect, these "units" reduce transportation (4,500 to 5,500 square feet can be loaded on a truck, compared to 1,100 square feet of full-bed masonry), installation and structural costs, allowing for a cost-effective project, compared to traditional cavity wall, full-bed masonry or stone applications.
"We saw the need – and the opportunity – to manufacture an all-weather tile that could be adhered to a suitable solid substrate,” says Craig Swirzon, CSI, thin-clad product manager of Cambridge, Ontario-based Arriscraft. “So we developed the Arris-tile range and jumped into the thin-veneer marketplace. However, not until we began partnering with Laticrete were we in a total comfort zone relative to installations.”
Swirzon worked together with Mark O'Keefe, Laticrete technical representative, specialty products division; Bob Duke, Laticrete technical support and training specialist, specialty products division; and Brad Bashford, owner of The Masonry Co. of Phoenix, Ariz., collectively assembling the optimal installation system with which to install the Arriscraft tiles. The Masonry Co. is a mason contractor licensed to complete all phases of masonry construction and specializing in adhering stone and brick veneer to the exteriors of large commercial projects.
"This project was completed by The Masonry Co. using cement board, Laticrete Air & Water Barrier, Latapoxy Waterproof Flashing Mortar, Laticrete Masonry Veneer Mortar, Laticrete Premium Masonry Pointing Mortar and, of course, the Arriscraft cladding,” says Mark O'Keefe. “Our products were applied in a number of exterior areas including those acting as an accent along the lower levels and at the grand entrance. Everyone was so impressed with the overall performance of the Laticrete MVIS, the hotel's interior fireplace was built using it, as well.”
O'Keefe went on to describe the MVIS products that comprised the system used. "An active, load-bearing material which protects buildings against water intrusion and the effects of extreme weather conditions, Laticrete Air & Water Barrier has been engineered for installation behind exterior wall claddings,” he says. “Contractors have the option to roll, brush or spray-apply it. Not only does it produce air and water holdout with vapor permeability, it can improve energy efficiencies and indoor air quality as well.”
"Latapoxy Waterproof Flashing Mortar," says O'Keefe, "is an epoxy-based waterproofing, and vapor barrier membrane used to waterproof seams, gaps or joints between a variety of substrates and metal and PVC pipe penetrations or flashing. It has been designed to be used with stone or brick for rapid installations that require a fast-curing waterproof flashing. It worked great around the hotel's windows, in particular.”
Laticrete Masonry Veneer Mortar is a patented, versatile, polymer-fortified mortar designed specifically for the installation of adhered masonry veneer, stone and thin brick. O’Keefe says it was an ideal choice for the hotel, as it provided maximum non-sag performance for the vertical installation, and offered optimal bond strength to the substrate.
"Laticrete Masonry Pointing Mortar, designed to be mixed with water or Laticrete Mortar Enhancer, is formulated from a blend of high-strength Portland cement, graded aggregates and colorfast pigments,” says O'Keefe. “This product provides a mortar joint that is dense, hard and durable, as can be witnessed firsthand at the Residence Inn."
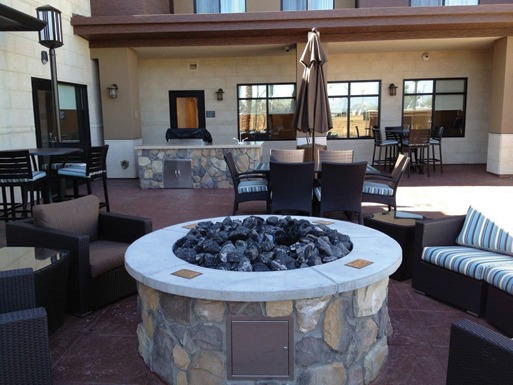
Owner Brad Bashford adds, "When we were hired by the general contractor, Porter Bros., for this project, we knew we would be facing some challenges. This was the first time we had ever seen a specification with Laticrete Air & Water Barrier used with a thin stone veneer; usually a waterproofing product like that is used being the building's exterior insulating and finish systems. And, this was the first time we were ever called on to use this Arriscraft product. It is absolutely amazing that this project turned out exactly as the two manufacturers, Laticrete and Arriscraft, advertise the performance of their products.”
Bashford says the building looks great with its combination of flat and split-face tiles, which were used as accent bands. He jokes that, as far as overall waterproofing goes, if it were to be dropped in a lake, it would probably float.
Fiber-mesh flashing materials were used around all windows, before the Laticrete waterproofing was applied. Before the actual installation began, Bashford and a team of his masons attended MVIS training sessions to get as familiar with the products as possible.
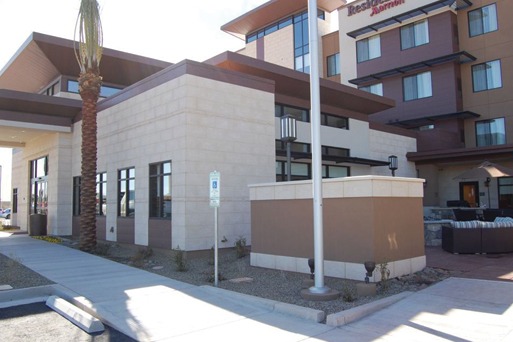
"Once we got into this project, we saw the incredible potential the MVIS offers to companies such as ours, and to our customers,” says Bashford. “Using materials that perform at this level, combined with the warranty, gave us peace of mind and certainly justified the expense.
"In particular,” he continues, “the property's ownership was extremely happy with the way the Arriscraft tile and the Laticrete MVIS material in the 3/8-inch grout joint worked side-by-side. They seemed to match perfectly."
O'Keefe says that, by using the MVIS, contract labor costs were reduced by one-third.
Return to Table of Contents