Flashing: Rules Never to be Broken
Words: Dan Kamys
Flashing
By Steven Fechino
The masonry industry is a proud group, building the most durable structures using time-honored techniques that have spanned generations. Discipline and mentoring are the keys to learning the rules that make up our complex trade.
As with all things, masonry has rules that will and will not change over time.
Rule No. 1 – Masons get paid for what they lay on the wall, not for effort.
Rule No. 2 – Completing a job correctly will cost the mason four-times less than a mistake. One: removal of defective work. Two: replacement of defective work. Three and four: the two jobs that were not completed while the repair work was performed.
Rule No. 3 – A wall without flashing completed properly has a 95 percent chance of leaking as opposed to a wall that is flashed correctly, which has almost no chance of leaking.
As a mason contractor you know all of this, so let’s discuss some of the new rule changes.
Sealants and flashing technology have improved in recent months. Products designed to improve the workmanship and quality over what has been available in the past are now available for both residential and commercial masonry contractors.
With many recent innovations, new flashing fabrics, membranes and composites have been created to give the masonry and roofing contractors better options to serve their building owners.
Early in my career, prior to the sealants that had evolved into what we see used today, bituminous mastics commonly were used to lap flashings, patch around dowels and seal penetrations that passed through the wall. Bituminous mastics, when used now, should be checked for compatibility with today’s flashings. When determining the compatibility between products, simply call the manufacturer and ask. Once your question is answered, request a letter stating the approval or disapproval of the product.
Sealants
Butyl
Butyl has had a long run in the construction industry, primarily due to the adaptability of the product to the roofing industry. Butyl, a synthetic rubber, is available in sealant tube form as well as convenient tape rolls. Butyl typically is more economical for the contractor to use in the correct application than some of the other sealants on the market.
When making a flashing lap or sealing around dowels, butyl is a smart choice. Butyl cannot be used for general joint sealing, expansion joints or any exposed joints, as this material remains uncured and loose for the life of the product. Butyl is compatible with today’s Polyvinyl chlorides, Thermoplastic Polyolefins, EPDM, Laminated Copper Fabrics and most Rubberized Asphalts.
Polyurethanes
Polyurethanes have been the sealant of choice by many masonry contractors to seal masonry-to-masonry, masonry-to-dissimilar material and flashing laps, and today’s polyurethanes are the most commonly used and accepted sealants for the mason contractor. Polyurethanes typically are one-or-two part sealants that offer a wide range of colors for many of your construction-related joint sealing.
Polyurethanes offer a life span ranging from six to 10 years, depending on exposure and geographical location. The working temperatures of polyurethanes are limited from 40 degrees to 95 degrees. The tack-free time of polyurethane is typically four hours. Single part polyurethanes typically are moisture cured, and the two part sealants are chemically cured.
Modified polyether (polyether)
Modified Polyethers have become a new force in the sealant industry. Polyethers are modified silicones that have the gunnability of silicone and the best characteristics of polyurethanes. Polyethers do not migrate oils into porous masonry and are gunnable in temperatures down to 15 degrees Fahrenheit. With the low VOCs and the quick tack-free time, polyethers soon will replace the polyurethanes used today,?? because of superior joint material performance and bonding to a wide variety of membranes and substrates, and the fact that they can be installed in a wide range of weather conditions. Polyether used with a primer will seal Thermoplastic Polyolifins with excellent results.
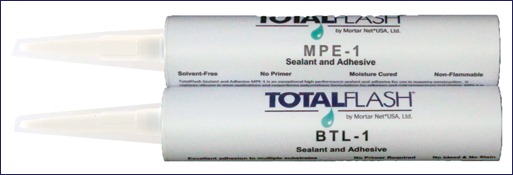
Flashings
Flashings have seen the biggest change in the market during the last few years, with the industry introducing products that have proved their value for many years in the roofing industry.
Copper laminate
Of course the tried-and-true copper laminate material we all used for years still is on the market. However, one major manufacturer now has made their product much more durable and desirable, by laminating a mesh of polyethylene on both sides of the copper. It is durable, nearly impossible to cut with a trowel and as good a material as any that can be found on the market. This is a premium flashing material that will perform well for years to come.?? Many of the copper laminates of today do not contain asphalt as a binder, and making them compatible with most building products.
Rubberized asphalt
Rubberized asphalt is the most common flashing on the market today, with several companies breaking up the geography of the United States. The rubberized asphalt, or “Stickie Back,” that is installed commonly is a good, stable material that performs well when installed properly. Primers are sold by some manufactures as part of every application, and other companies will omit the primer if the customer used a term bar. Installation of this membrane should be discussed with your project architect and manufacturer prior to installation. It is critical that the mason contractor read the fine print for each product as warranties can depend on the use of primers and full adherence to the substrate.?? Rubberized asphalt is ultra violet (UV) sensitive. Therefore, extended exposure to sunlight is not recommended. Compatibility between rubberized asphalt and PVC-molded corner boots and end dams should be investigated prior to construction as plasticizers can migrate from the PVC and reduce the plasticity of the rubberized asphalt over time. This causes the potential for a leak down the road. Metal drip edges typically are used at the face of the wall when installing rubberized asphalt as many manufacturers require that the membrane be held back from the brick face +/- ?? inch.
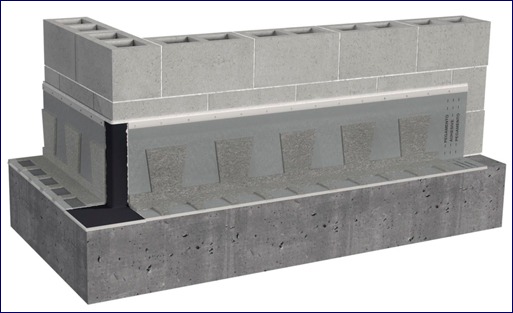
Polyvinyl chloride (PVC)
Today’s PVCs combine old and new technology to create strong, durable and flexible materials, thanks to the addition of non-migratory plasticizers. That means the material that makes it stable is going to stay within the PVC and not leach out, evaporate or allow the PVC to break down and become brittle, which would allow cracks and create leaks. PVCs are as good a membrane as any on the market. A crossover from the roofing industry, the masonry industry has allowed the roofing industry to test market roofs all around the world for many years to prove the durability, workability and economy of such a membrane.?? I started this article stating that masons are proud; they are smart, too.
Compatible with many polyurethanes, polyethers and butyls, PVC is the first choice for many contractors when they need to get it right the first time.
Thermoplastic polyolifin (TPO)
TPO is another product that we inherited from the roofing industry. TPO is a flexible membrane that has a th30-year life span when installed on a roof, and an unlimited life span when placed in the cavity of a building. TPO has an advantage over all other membranes on the market, because you can seal the laps using a butyl sealant or primed polyether. You can also hot–air weld them, which is a process commonly known as heat-welding. This can provide a joint completely bonded by hot air. I understand that “heat welding” may be a new term to some, but the simplicity of the effort gives unbelievable results.
In a demonstration that I performed for Tom Sourlis, owner of Mortar Net USA Ltd., we heat-welded a two-foot section of TPO in just a minute or so, and water tested it several minutes later with positive results – no leaks. Low-cost equipment for heat-welding can be purchased for under $100 and would reduce the sealant requirements for installing flashing by ??- to 10.3-ounce tube per lap. Unprimed polyethers and polyurethanes cannot be used for sealing this membrane, as surface energy of the membrane will not allow a durable, long-term bond.
Ethylene propylene diene monomer (EPDM)
EPDM is another roofing crossover material that has entered the masonry industry during the last several years. EPDM is flexible and easy to cut, and will easily install as it has little memory to the roll in hot or cold temperatures. EPDM is a rubber that responds well to certain polyethers and butyls as a lap sealant and general installation sealant. It is not compatible with PVC-molded corner boots or end dams. EPDM must have similar EPDM components for terminations and corners applications, and it is compatible with most air barriers on the market.
Other improvements in the flashing industry include the advancement of unitized flashing solutions. Unitized flashings are single-component flashing systems that can be offered with any of the different flashing membranes that have been discussed. Inclusions to the system consist of a membrane, pre-designed laps, screws, weeps, termination bar, drip edge and a mortar collection device that has passed the requirements of the ASTM E-514 water test. Unitized flashing solutions also come with manufacture-supplied, pre-engineered flashing take offs, special-cut panels for window and door heads delivered to the jobsite, and technical supervision and training. This additional service is provided by one flashing system manufacturer for no additional expense to the project. Unitized flashing can carry a premium cost. However, the economic benefits have been proven over the years with no failures reported.
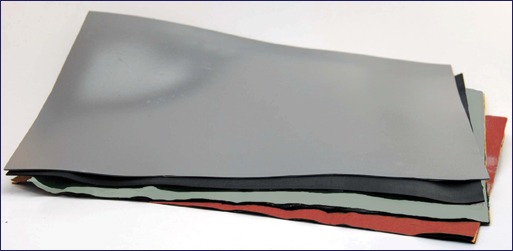
New to the market this spring is the roll flashing that has been made with the mortar collection system attached directly to the membrane. With clean lap spaces available every six inches and weeps built into the roll, the TotalFlash Roll product has taken off like it was shot from a cannon. The membranes offered for the TotalFlash Roll Solution are any of the membranes and composites that were discussed earlier, which allows the design or construction team to choose the correct membrane for the project.
Manufacturer support for the TotalFlash Roll Solution can include a manufacture pre-engineering flashing quantity take-off and personal technical assistance to aid the mason contractor with installation support.
All of the flashing membranes mentioned in this article are compatible with all of the high-loft, non-woven and unilateral mesh products used in mortar-collection devices and mesh-wall fabrics that cover the entire inner wythe of the structure.
It is critical that the wall mesh not be placed behind the termination bar. Placement of the mesh should extend over the termination bar and lap about one inch over the flashing.
The last major improvement observed in the sealant and flashing market is that contractors now can obtain answers to their technically based questions, regarding anything masonry. One of the companies, Mortar Net USA LTD is offering flashing solutions and has created a specialized staff to answer questions posed by the mason contractors regarding all masonry questions. Today’s technical departments are free to the design and construction personnel answering anything masonry.
As with any industry, parts of the flashing and sealant industry constantly are changing the rules for the benefit of the design and construction team found on many of the projects that you currently work on. We are trying to help mason and roofing contractors by preventing one leak at a time.
Return to Table of Contents