Masons Guide To Job Site Handling And Maintenance Of Architectural Cast Stone
Words: Jan Boyer
Words: Jan Boyer, Executive Director, Cast Stone Institute
The knowledge of the mason about architectural cast stone is crucial to assuring a quality project for the owner, architect and general contractor.
The first thing to consider when working on a job that involves architectural cast stone is to get good quality product from a Certified Cast Stone Institute Producer. Once the quality product arrives on the jobsite, there are things to know about jobsite handling, installation, cleaning and long term maintenance of the cast stone that will impact the project into the future. There are also naturally occurring situations with cast stone, much like other cement based products, that can be addressed while the project is ongoing or after completion.
The following items addressed are topic driven and snapshots of technical information that is available through Cast Stone Institute Specification, Standards and Technical Bulletin documents which are readily available for your reference.
JOB SITE HANDLING AND INSTALLATION

An extensive checklist was developed for the handling, storage and installation of cast stone. Storage of cast stone on the job site should be above ground on non-staining planks or pallets and away from heavy construction traffic. Cast stone stored for an extended period of time should be covered with non-staining tarps.
Specific installation considerations for the mason referenced in this technical bulletin include: ensuring climate conditions are compatible with the mortars; setting with full mortar joints; filling all dowel holes and anchor slots; installing flashing and damp proofing; using only non-corrosive anchors; assuring that weep holes are installed over windows, at relieving angles and at the bottom of walls and more. The additional requirements for installation are included in the TMS 404-504-604 Standards for Architectural Cast Stone Design, Fabrication and Installation.
After setting, the columns, pilasters, entry jambs, windowsills and all cast stone with projecting profiles should be protected with non-staining materials during the remaining construction to protect the cast stone. Reference Technical Bulletin # 37
TOUCHUP AND REPAIR (Use photo of repair)
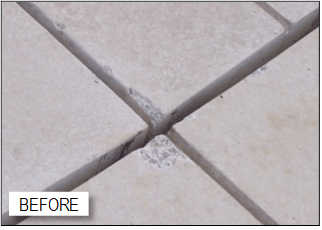
Even with special care and protection, cast stone may become chipped from time to time and therefore a certain amount of touch up is to be expected. Any chip obvious from a 20 foot distance should be touched up with material provided by the cast stone manufacturer. The stone mason should include touch up as part of the ordinary pointing and wash down operations prior to final inspection.
The procedure for repair will include dressing the damage and applying fresh material to achieve the desired finish and shape, covering the repair with a wet rag and/or plastic cover, to prevent the water from evaporating before the cement is hydrated. Climate conditions may affect the touch up, therefore, do not repair cast stone in freezing weather. On hot sunny days repairs should be done during the morning hours where the cast stone is shaded or at temperatures less than 90 degrees Fahrenheit.
General instructions for touch up and repair are on the Cast Stone Institute website http://caststone.org/bulletins/patching.htm. We recommend that you contact the cast stone fabricator for repair materials and instructions for their product.
A properly executed repair will not match in color immediately. Dry tamp produced cast stone will appear lighter where repaired, while wet cast produced cast stone may appear darker. Repairs, matching immediately or in two or three days, have a tendency to change color later on after weathering. This process could take three months to a year or longer depending on the climatic conditions and exposure to the weather.
Reference Technical Bulletin #38
CLEANING

For new building construction it is recommended that a cleaning procedure, using the appropriate cleaning agent and method, be performed to remove any debris and efflorescence. The most common stains due to construction are dirt, mortar smears and efflorescence. A general rule of thumb is to use the least aggressive cleaning material and method to clean the building. Dirt can be removed by scrubbing with a mild detergent and water and thorough rinsing.
The most important step to stain removal is identifying the stain and its cause. Any treatment should be tested in a small inconspicuous area prior to cleaning the main wall. A key recommendation is to be very careful of the final cleaning of the structure that has dark materials – brick or block - above the light colored cast stone, as the dark will wash down over the light cast stone and cause discoloration.
Direct high pressure power washing and sandblasting are not recommended procedures for cleaning cast stone. Furthermore, metal fiber brushes, rubbing stones and any tool or device that can scar the cast stone not to be used for cleaning cast stone. Technical Bulletin #39
MASONRY STAINING
Improper cleaning techniques, staining from other construction products, or color variations may require cast stone staining. This procedure can unify the color throughout and remove wanding marks, graffiti or other related concerns. An expert in masonry color matching should be contacted in this instance.
INSPECTION AND ACCEPTANCE
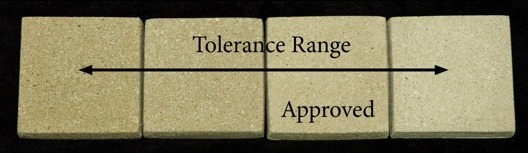
The inspector should be familiar with the cast stone specification and contract documents, then check the color and texture of the approved sample against the delivered product. When dry, the cast stone should approximate the color and texture of the approved sample when viewed under typical lighting conditions and show no obvious imperfections other than minimal color and texture variations from a 20 foot distance. Minor variations in color and texture should be expected within limits of the approved range of samples. Some projects will show more color variation than others depending on the type of cement, integral color and cleaning procedures.
The inspector and/or mason should also be familiar with the dimensional requirements of the installation as they pertain to joint sizes and interfaces with other materials. Wherever possible, an investment should be made in mockup panels and/or sample units. The technical bulletin includes a listing of common deficiencies which are typically not acceptable in high quality cast stone. Reference Technical Bulletin #36
__________________________________________________________
Now, let’s look at naturally occurring situations after the initial construction and how they can be mitigated.
CRAZING
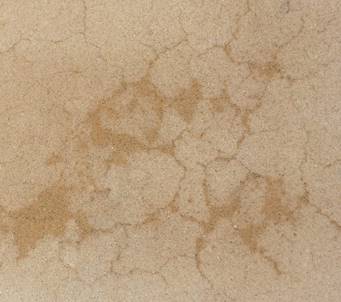
Crazing is defined as fine and random cracking extending through the surface, normally less than one millimeter in depth. Crazing does not affect the structural integrity of the concrete and should not by itself be cause for rejection.
Remediation
Since crazing is only on the surface, the visual appearance of the cracks can usually be minimized by cleaning the affected areas with a mild acid solution. Severe cases of crazing may require application of a silane/siloxane sealer, following cleaning, to penetrate the cracks and to keep dirt from settling into the surface. Reference Technical Bulletin #32
EFFLORESCENCE
Efflorescence is a crystalline material, usually white, that forms on the surface of masonry walls and concrete products. While unsightly, it does not affect the structural integrity of the cast stone. It is generally caused by moisture related issues in the wall from a variety of sources. It is difficult to predict whether efflorescence will occur, but it is generally in the fall and winter months. The sooner it is removed the better.
Remediation
Planter, fountain and swimming pool coping, treads, risers, stone pieces and pavers may be treated with a silane or silane/siloxane water repellent coating on the surfaces that are above grade. For below grade applications, a damp proofing product, such as a cementitious waterproof backing or bituminous damp proofing may be applied to the back, sides and the below grade face surfaces. This will minimize the likelihood of dirt and groundwater entering the surface of the stone; a frequent cause of staining, efflorescence and enhancement of crazing. Check that the water repellent coating does not affect color or texture when dry. Reference Technical Bulletin #33
WATER REPELLENT COATINGS
The purpose of a water repellent coating should be to minimize water intrusion through the outer surface of the cast stone or mortar, while allowing sufficient vapor transmission to let moisture out of the wall cavity, thereby improving weathering qualities. Water repellent coatings are not a remedy for moisture penetration problems caused by poor details such as the improper use of flashing, lack of weep holes, non-ventilated wythe, failure of joint materials or the a use of hard mortar joints where sealant joints should be used.
Remediation
Proper application of water repellents can minimize efflorescence, mildew, staining and dirt. When a water repellent coating is desired, the Cast Stone Institute® recommends using a silane or siloxane (or blends of each). Water repellents should be applied after all pointing repair, cleaning and inspection operations are completed. The application should be guaranteed by the water repellent manufacturer or the applicator not to discolor the cast stone. Reference Technical Bulletin #35
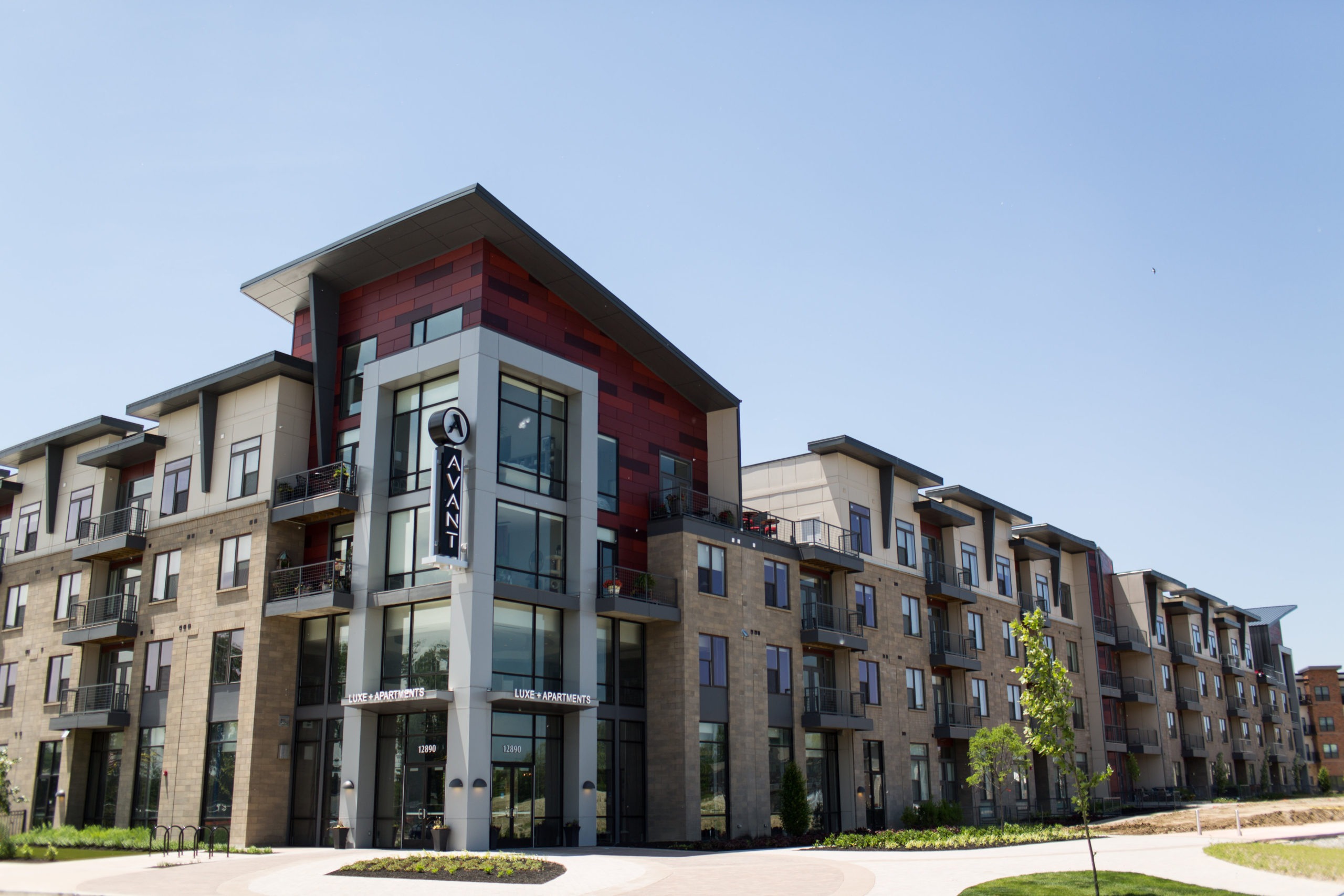
_________________________________________________
It is important to remember that architectural cast stone is specified, fabricated and installed under legal reference standards documents and not just CSI industry standards.
PRIMARY REFERENCE DOCUMENTS
ASTM C1364-19 Standard Specification for Architectural Cast Stone
TMS 404-504-604 Architectural Cast Stone Standards for Design, Fabrication and Installation
(Note that both of these are legal documents and are referenced in the International Building Code.)
Specification 047200 Standard Specification for Architectural Cast Stone
caststone.org/specifications.htm
Cast Stone Institute Technical Bulletins -- caststone.org/bulletins.htm
Properly manufactured, designed and installed, cast stone can result in an architectural project of enduring beauty to be enjoyed for 100 years. When specifying cast stone on a project, be sure to call out a Cast Stone Institute Certified Producer Member as this provides the owner the quality cast stone the project deserves.
________________________________________________
Jan Boyer has been the Executive Director of the Cast Stone Institute since 2006. She currently serves on the Board of Directors for the Masonry Alliance for Codes and Standards (MACS) as Board Secretary and serves on committees for The Masonry Society as well as the TMS 404-5-4-604 Committee. She also sits on the ASTM C27.20 Committee under which Architectural Cast Stone is referenced. She can be reached at jboyer@caststone.org
All photos courtesy of the Cast Stone Institute ®