Case Studies: Rehab and Restoration
Words: Dan Kamys
Case Study: Rehab and Restoration
Collegiate sports are highly competitive, and to attract fans and top recruits, facilities have to be kept up to date and offer the highest levels of amenities. The University of Tennessee launched a multi-phased renovation program of their baseball stadium in 2006. Phase II of the renovation of Lindsey Nelson Stadium included new brick fa??ade to create the look and feel of a major league stadium.
When built in 1992, the original stadium was precast concrete, painted green. The renovation design called for creating a new look that was in keeping with the overall campus atmosphere, attract the nation’s top recruits, be timely to avoid any delays in the baseball schedule, and be well-received by the fans for years to come. The decision was made to brick the existing fa??ade.
The architects for the project, Lindsay & Maples, Architects Inc. investigated using full brick, but due to structural load evaluations, elected to use thin brick. Weight and added dead load was a major consideration. In order to prevent performing an expensive and time-consuming structural analysis, added weight had to be minimized. By selecting thin brick veneer, added weight was kept below 10 psf. The use of thin, adhered veneer over full-bed masonry also eliminated any egress isle space issues because the 1/2-inch thickness of thin brick had minimal effect on space.
After careful consideration, thin brick from General Shale Brick was selected. Several parties were involved in the decision, including the architect Rick Lindsay of Lindsay and Maples in Knoxville, Tenn.; university administration; and even the baseball coaching staff.
“By using the thin brick, we were able to overcome weight and structure issues and still honor the owner’s desire to have the look of brick,” says Rick Lindsay, project architect.
To assure that the renovated stadium was part of the integrated design of the campus, university officials selected the same style brick used on many of the university’s structures: Campus Blend. The brick was cut thin to 1/2-inch by General Shale Brick and shipped to site for installation. Garrett Masonry, Knoxville, Tenn., completed the installation in time for the beginning of the season.
“I appreciated all the teamwork from the owners, architect, and material suppliers,” says Steve Garrett, Garrett Masonry. “The product went up well, and I was proud that I was able to contribute to the enhancements of the university’s facilities.”
Several thin brick installation methods were considered, but it was ultimately decided that a direct adhered veneer system would be used in accordance with the ACI 530.1/ASCE 6/TMS 602 Building Code Requirements for Masonry Structures section 6.3.2. Additionally, a Laticrete thin set system using tile installation guidelines in ANSI A108 (American National Standard for Installation of Ceramic Tile) and the TCNA (Tile Council of North America) Handbook for Ceramic Tile Installation was selected.
Jason Cathey, P.E., from Rouse Construction Co., was the project engineer for the renovation. “The renovation to the University of Tennessee Lindsay Nelson Baseball Stadium was our first experience with the Laticrete products,” Cathey says. “Not only did they provide good technical phone support and product literature, they also provided on-site training and installation observations to ensure proper application. Rouse Construction Co. built the original stadium in 1992, and with using quality building products, we are confident that the owner will continue to be satisfied with their facility for years to come.”
A direct adhered method was chosen to provide the most durable installation, since bonding directly to the existing precast concrete substrate eliminates mechanical fasteners or lath that could be susceptible to corrosion or failure. A Laticrete Hydro Ban membrane was also installed, which gave the entire system a 25-year warranty from Laticrete. Since this was, primarily, a vertical installation Laticrete 255 thin set was specified due to its high initial “grab” bond and no-sag properties. To prepare the existing painted precast concrete surface for installation, the specification called for sandblasting.
To complete the project in time for the upcoming spring schedule, it was necessary to perform the installation during the winter months; thus, it was important to strictly observe cold weather installation guidelines. The project specification called for Cold Weather Requirements in accordance with ACI 530.1/ASCE 6/TMS 602. Garrett Masonry did an excellent job of monitoring temperatures, tenting the structure and using supplemental heating when required.
The masonry crew from Garret Masonry was conscientious and had the work area tented, dry, and heated with a salamander unit to keep the area (and substrate) between 63 and 68 degrees Fahrenheit. A thermometer was located inside the tented area and monitored as the work progressed. A waterproof membrane was applied to the substrate and a skim coat of 255 thinset adhesive was applied to the surface. Measuring buckets present at the mixing station, the 255 and mixing water were kept inside the conditioned work area.?? Installers removed dust from the back of the brick with a sponge and water before installation. Also, the installers made a practice of “keying in” the mortar with a mason’s trowel before the mortar was notched; the bricks were being “backbuttered” as well. Spacers were used in succession and were removed after the mortar was set up enough to hold the bricks in place and placed in the subsequent courses. The masonry crew seemed pleased with the tenacity of the mortar, and demonstrated how well the early bond strengths were by trying to pull one of the bricks off that were installed the prior day off, it did not move.
In conclusion, the use of adhered thin veneer allowed the University of Tennessee to obtain the desired aesthetic look they wanted, overcome issues with weight, minimize impact on egress spacing, and complete the “new” stadium in time for opening of the baseball season.
Return to Table of Content
Case Study: Rehab and Restoration
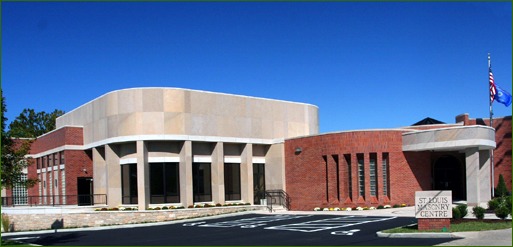
With the nation’s financial markets on the verge of collapse, panic and fear were sweeping the nation in the fall of 2008. St. Louis’s construction industry was especially hard hit. Numerous projects were postponed, and the industry began hemorrhaging jobs.
These were the bleak conditions confronting the leadership of the St. Louis Mason Contractors Association as they wrestled with a decision on their pending plans for the major expansion and renovation of the Masonry Center, their Richmond Heights headquarters at 1429 S. Big Bend.
The ongoing background turmoil complicated their decision. No one questioned that the 1950s-era structure had to be replaced. Not only was it too small, but also it hadn’t been upgraded in 25 years and could no longer serve the needs of the MCA and its sister organization, the Masonry Institute of St. Louis, also located in the building.
But with the local construction industry spiraling downward, the MCA’s officers knew they couldn’t play it safe and put the project on the shelf. Too much was at stake. “We felt we owed it to the St. Louis masonry industry to go ahead with our plans and provide jobs,” says Richard F. Frisch Jr., president of the MCA and owner of Frisch Masonry in Kirkwood.
“It would have been easy to put the project on hold and wait until things got better,” says Jeffrey D. Schmidt, MCA VP and owner of JDS Masonry in St. Charles. “Instead, we decided to show our commitment to the industry and its future by putting people to work.”
The $2.1-million project, which was completed in October, effectively doubles the building’s size while modernizing its facilities. The expansion, designed by local architects at Archimages, features a meeting/presentation room that can seat up to 200 or be divided into two rooms that can accommodate 90 persons each. The expansion also includes additional office space, a larger boardroom, a larger library/study room, and modern restrooms.
“I think the real story is that when the economy was at its darkest and everyone was afraid we might be looking at Armageddon, the board decided to go ahead with the project,” concluded David A. Gillick, MCA executive director.?? “The MCA has been at the heart of the St. Louis masonry industry since we were chartered in 1896. Going forward with the project and the jobs it provides is our way of showing that we remain committed to the industry and its future success.”
Return to Table of Content
Case Study: Rehab and Restoration
Preserving and restoring Vermont’s majestic Shelburne Farms means that masons, apprentices and interns must analyze historic processes and materials, and use technology to recreate objects and create fresh treatments.
In 1886, members of the wealthiest family in America, the Vanderbilts, began creating a model agricultural estate in Vermont, overlooking Lake Champlain. Dubbing it “Shelburne Farms,” they hired two of the nation’s most famous planners: Frederick Law Olmsted Sr., the “father of landscape architecture,” and architect Robert H. Robertson. The property featured innovative agricultural and land-use practices, plus a horse-breeding enterprise and a grand family residence.
But over the years, the family’s fortunes changed, and the farm’s majestic structures were neglected. In 1972, the site became a non-profit environmental education center.
Today, Shelburne Farms is a 1,400-acre working farm (its dairy herd produces fine cheeses) and a National Historic Landmark. It has become a magnet for New England’s top historic preservationists. Their presence attracts talented summer interns and apprentices, eager to acquire hands-on experience.
Douglas Porter is the site’s architectural conservator and project manager. He has a M.S. degree in Historic Preservation and holds a research faculty appointment at the University of Vermont’s School of Engineering.
Porter feels a powerful bond with past builders. “Much of what we do in historic preservation is dictated by artisans who are long gone,” he says. “I think of them whenever I work on a project. And when we train new craftspeople, we’re extending the past into the future.”
That training often includes exposure to scientific methodologies. Any given project might entail: geotechnical assessments of below-ground conditions; laboratory analysis of old brick, mortar and concrete; 3-D laser-scanning of existing decorative elements, for accurate replication of lost or damaged pieces; testing of new treatment formulas (which Porter says has led to improved methods for repairing cast stone); and new technologies as they emerge.
Currently, Porter is overseeing restoration of the Farm’s Formal Garden, which lies between Shelburne Inn and the lake bluff. This article focuses on the brick wall of its central feature, a fountain and pool.
Restoring the Fountain Wall
The fountain wall, built in 1914, is a solid, three-wythe brick retaining wall, set in a Flemish bond. Oddly, it had been built without a concrete back wall. Thus, the bricks in direct contact with the soil had decomposed badly. (Throughout the Formal Gardens, nearly 12,000 bricks would eventually be replaced.)
The project team included four masons with strong preservation experience: James Duggan, Preservation Unlimited, Montpelier, Vt.; Ryder Owens and Rae Berolzheimer, Petra Terra, Wilmington, Vt.; and John Wastrom, Portsmouth, N.H., plus an equal number of interns, apprentices and laborers.
They carefully dismantled the brickwork, salvaging as many bricks as possible for cleaning and reuse. A reinforced concrete wall was erected to prevent future brick deterioration.
They got a lucky break during their search for replacement bricks. A nearby salvage company had what seemed to be the same type of brick used in the original wall, and even made by the same manufacturer, Drury Brickyard (1850s – 1970s). Porter had samples of the replacement bricks tested for soluble salt content, compression strength and modulus of rupture. They passed nicely. And, since the original mortar had held up well, the project team duplicated it.
The team needed to decide how to flash the wall’s deep, curved cavity. Among their options was an innovative, all-in-one cavity-drainage system, TotalFlash. It contained multiple drainage components and all necessary installation hardware, factory-assembled onto handy-sized panels of flexible flashing. They asked the manufacturer, Mortar Net USA, of Burns Harbor, Ind., whether it could be made to fit behind the fountain’s geometrically unique brickwork.
Earl Bickett, general manager of Mortar Net, agreed to custom-produce TotalFlash panels that would be twice the standard height, and to omit the usual stainless-steel drip-edge (which would be fabricated locally, to match the wall’s curvature).
After further research, the team decided TotalFlash best met their technological standards. When the factory-assembled panels arrived and were installed, Porter was pleased. Everyone had learned something new.
During bricklaying, care was taken to replicate the wall’s original appearance in every detail. The arched and circular patterns were turned over templates based on historic photographs. The restored walls were tied to the concrete retaining walls using stainless-steel ties and standards as anchors.
When they finished, the team could almost hear ghostly applause from the original architect.
Porter still has many projects ahead of him at Shelburne Farms. They will all demand a good bit of science before and during the actual labor. But you can tell he loves unraveling the mysteries of long-dead builders and far-outdated materials.
“Many historic trade-processes have been lost,” he says. “Our job is to figure out what they were, why they worked, and how to duplicate them?Ķwithout leaving any fingerprints.”
Return to Table of Content